Themenübersicht
Die Produktionsaufträge bilden die Basis für den gesamten Produktionsprozess. Sie können manuell erfasst, auf Basis von einer Materialbedarfsplanung erzeugt oder über den Datenimport im System entnommen werden.
Die Einlastung kann in folgenden Anwendungen ausgeführt werden:
- Produktionsaufträge
- Cockpit: Produktionsaufträge – für mehrere Produktionsaufträge
- Produktionsvorschläge
Die Einlastung von Produktionsprozessen besteht darin, die erforderlichen Materialbuchungen, Arbeitsgänge und Ressourcen zu erfassen. Die Einlastung erfolgt unter Bezugnahme der zugrunde liegenden Stücklisten, Arbeitspläne und Produktionspläne.
Die Terminierung aller Kapazitäts- und Materialbestandsteilen erfolgt gemäß dem ausgewählten Terminierungsmodell, das für den entsprechenden Produktionsauftrag definiert wird.
Die Einlastung ist nur für Produktionsartikel mit dem Status Freigegeben möglich. Der Status des Artikels ist in der Anwendung Artikel → Ansicht Produktion → Feld Verwendungsstatus. Die gesperrten Artikel bzw. die Artikel mit dem Löschkennzeichen werden nicht freigegeben.
Bei der Einlastung des Produktionsauftrags werden über die Schaltfläche [Aktion wählen] → [Einlasten] folgende Aktionen durchgeführt:
- Es werden Materialbuchungen für alle eingelasteten Positionen aus der Stückliste erfasst.
- Es werden Materialbuchungen für alle eingelasteten Positionen der Kuppelprodukte aus der Stückliste erfasst.
- Für alle eingelasteten Ressourcen werden Ressourcen-Reservierungen erzeugt.
- Für alle Fremdfertigungs-Arbeitsgänge werden Beschaffungsaufträge erfasst.
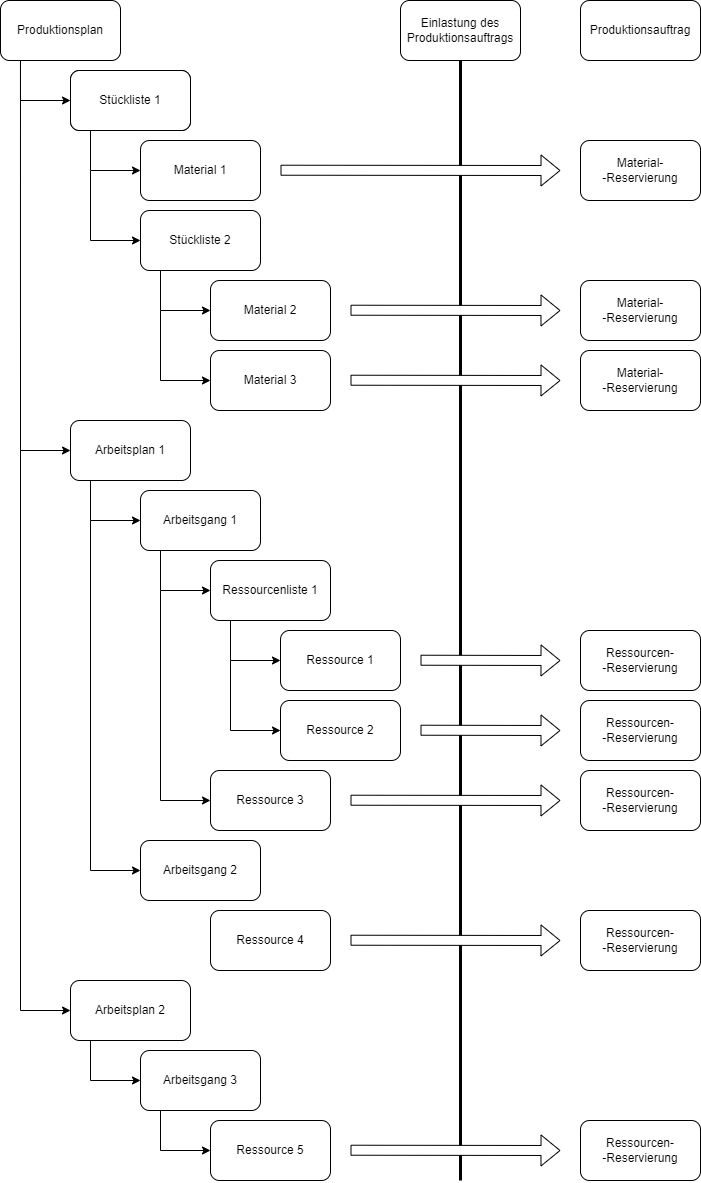
Details zur Einlastung eines Produktionsauftrags
Folgen der Einlastung eines Produktionsauftrags:
- Die Einlastung mit Kapazitätslimit hat Vorrang vor definierten Abhängigkeiten in der Struktur des Produktionsprozesses.
- Mit dem Kapazitätslimit können Sie die Laufzeit eines Produktionsauftrags und damit die Zeit für die Reservierung von Ressourcen steuern. Die Kapazität für die Ressource ist über die Anwendung Ressourcen, Arbeitsgänge und Arbeitspläne eingestellt. Im Bezug auf das Kapazitätslimit einer Ressource für die Freigabe ist es möglich, die folgenden Berechnungen gemäß der folgenden Warnung zu nutzen:
- Die Berechnung der Kapazität der Ressource auf Basis der Daten im Arbeitsgang und Arbeitsplan. In diesem Fall ist die Kapazität, die in der Anwendung Ressourcen definiert wurde, ignoriert. Die Kapazitäten, die für die Ressourcen in den genannten Anwendungen definiert wurden, werden beim Start multipliziert.
- Die Berechnung der Kapazität der Ressource auf Basis der Stammdaten der Ressource, sowie des Arbeitsgangs und Arbeitsplans. Alle Kapazitäten werden beim Start entsprechend multipliziert.
- Die für den Arbeitsplan definierten Abhängigkeiten wirken auf die Transport- und Pufferzeiten aus, wenn sie auch im Arbeisgang verwendet werden.
- Die verwendeten Produktionsstrukturen werden immer durch das Datum bestimmt, das im Feld Einlastungsdatum auf der Registerkarte Einlastung der Anwendung Produktionsaufträge definiert ist. Bei der aktiven Versionierung von Produktionsdaten werden nur Versionen verwendet, die zu einem bestimmten Datum freigegeben sind oder waren. Dazu gehören Stücklisten, Arbeitsgänge (Fremdfertigungs-Arbeitsgänge), Arbeitspläne und Produktionspläne.
- Wenn Kuppelprodukte in der Anwendung Produktionspläne keinem Arbeitsgang zugeordnet wurden, beginnt ihre Produktion, wenn der Produktionsauftrag abgeschlossen ist.
- Bei einer Position des Fremdfertigungs-Arbeitsgangs prüft das System, ob bereits eine Bestellung angelegt wurde oder ob ein Wareneingang stattgefunden hat. Wurde bereits eine Bestellung erzeugt oder der Wareneingang zu dieser Bestellposition gebucht, bleibt die ursprüngliche Bestellposition erhalten und muss manuell storniert oder durch eine Bestellanpassung entsprechend angepasst werden.
- Wenn einem Arbeitsgang eine Ressourcengruppe zugewiesen ist, wird eine verfügbare Ressource aus der Ressourcengruppe automatisch beim Start ausgewählt. Bei Ressourcengruppen wird immer ein Kapazitätslimit verwendet, unabhängig von dem ausgewählten Terminierungstyp.
- Gemäß dem Arbeitszeitmodell, dem ein Feiertagsmodell zugeordnet wurde, erfolgt die Ermittlung des Kapazitätsprofils. Wenn dem Wochenzeitmodell kein Feiertagsmodell zugeordnet wurde, gelten die für den Werkskalender definierten Feiertage. An Feiertagen ist keine Produktionskapazität verfügbar.
- Lagerorte
- Zugangslagerort – das Lager, in das der hergestellte Artikel geliefert werden soll. Die wird entnommen aus:
- der Kopfzeile der Anwendung Stücklisten
- der Ansicht Produktion, Sektion Produktionsdaten in der Anwendung Artikel für den Artikel, der herzustellen ist
- der Anwendung Produktions-Auftragsarten
- Abgangslagerort – das Lager, aus dem das Material für die Produktion entnommen wird, wird bei der Materialbuchungsposition oder im Editor der Position der Stückliste eingegeben. Für das Kuppelprodukt wird es als Eingangslagerort gelten.
- Ausschussfaktor – führt zu einem Anstieg der gebuchten Materialien und zu einer Senkung der Menge der Kuppelprodukte. Die Menge wird nach der folgenden Formel berechnet:
- Die Transportzeiten der ersten Arbeitsgänge werden bei der einstufigen Einlastung nicht berücksichtigt.
- Für jede Position des Produktionsauftrags sind die angegebenen Bedingungen, Formeln und Ersatzfunktionen in Produktionsstrukturen (Arbeitsgänge, Arbeitspläne, Stücklisten) sichtbar. Die Ausnahme sind die Pufferzeiten.
- Es ist nicht möglich, Hauptbedingungen und Ersatzressourcen zu ändern oder neu anzulegen. Nur Formeln, nicht aber Bedingungen, können direkt auf den Auftragspositionen manuell bearbeitet werden.
- Die Berücksichtigung der manuell geänderten Formeln erfolgt bei der Neuberechnung von Termin und Menge über die Schaltfläche [Termin und Menge ändern] in der Anwendung Produktionsaufträge.
- Die Pufferzeit wird mit der Aktion Termin und Menge ändern entsprechend der für den Arbeitsgang eingestellten maximal möglichen Reduzierung der Pufferzeit neu berechnet. Die Aktion ist über die Schaltfläche [Termin und Menge ändern] in der Anwendung Produktionsaufträge verfügbar.
- Die Bearbeitung der Abhängigkeiten für Arbeitsgänge ist über den Positionseditor in der Anwendung Produktionsaufträge möglich. Die Berücksichtigung der manuell geänderten Abhängigkeiten erfolgt bei der Neuberechnung von Termin und Menge über die Schaltfläche [Termin und Menge ändern].
- Die Bearbeitung der Parameter ist über den Positionseditor in der Anwendung Produktionsaufträge möglich:
- für variable Parameter, die für die Ressource bzw. Ressourcengruppe in der Anwendung Ressourcen und Ressourcengruppen definiert wurden.
- für Parameter der Arbeitsgänge, die für Arbeitsgänge in der Anwendung Arbeitsgänge definiert wurden.
Die Berücksichtigung der manuell geänderten Parameter erfolgt bei der Neuberechnung von Termin und Menge über die Schaltfläche [Termin und Menge ändern].
- Der Text der Materialbuchung wird aus dem Positionstext der Stückliste übernommen.
- Der Text der Arbeitsgangsposition wird aus dem Positionstext des Arbeitsplans übernommen. Gibt es keinen Text, wird der Basistext aus dem Arbeitsgang übernommen.
- Der Text der Ressourcenreservierung wird aus dem Positionstext des Arbeitsgangs übernommen. Gibt es keinen Text, wird der Text aus Stammdaten der Ressource übernommen.
- Der Text der Position der Kuppelprodukte wird aus dem Text der Position der Stückliste übernommen.
- In einem Produktionsauftrag ist es auch möglich, die Termine mit der Aktion [Termine neu berechnen] neu zu berechnen. Die Auswirkungen der Aktionen:
- die manuellen Änderungen in Mengen und Zeiten werden beibehalten
- Kapazitätslimit bleibt unverändert
- es werden die angegebenen Abhängigkeiten berücksichtigt
- die Änderungen an Formeln und Parametern werden nicht berücksichtigt
Terminierungsarten und Einlastungsmethoden
Die richtige Festlegung der Terminierung in der Anwendung Produktionsaufträge hat Einfluss auf die Festlegung von Zeiten und Abwicklungsdatum des Produktionsauftrags. Die folgenden Terminierungsarten können unterschieden werden:
- vorwärts ohne Kapazitätslimit
- vorwärts mit Kapazitätslimit
- rückwärts ohne Kapazitätslimit
- rückwärts mit Kapazitätslimit
Darüber hinaus werden bei Produktionsaufträgen die folgenden Einlastungsmethoden verwendet:
- einstufig
- mehrstufig
- mehrstufig im Auftrag
Aus diesen Zusammenhängen ergeben sich die folgenden Auswahlmöglichkeiten für die einstufige Einlastung:
- Vorwärts einstufig ohne Kapazitätslimit
- auf der Grundlage des festgelegten Beginndatums wird das (frühestmögliche) Enddatum berechnet
- der Auftrag wird so schnell wie möglich eingelastet, was die Übergangszeit der Halbfabrikate beeinflusst, die nicht auf dem kritischen Pfad liegen
- die Kapazitätslimite werden nicht berücksichtigt
- Rückwärts einstufig ohne Kapazitätslimit
- Einlastung so spät wie möglich
- minimale Zeit für die Bearbeitung
- Übernahme der Lücken in der Arbeitskraft
- die Kapazitätslimite werden nicht berücksichtigt
- Auf der Grundlage des festgelegten Enddatums wird das Beginndatum berechnet
- der Produktionsauftrag wird so spät wie möglich eingelastet
- der Produktionsplan wird von der letzten Position aus eingesetzt
- Vorwärts einstufig mit Kapazitätslimit
- ermöglicht die frühestmögliche Einlastung unter Berücksichtigung der Ressourcenkapazität (Einsatz und Buchung)
- Die Terminierung erfolgt auf der Grundlage der verfügbaren Ressourcenkapazität Mangelnde Materialverfügbarkeit hat keinen Einfluss auf die Terminierung
- Auf der Grundlage des festgelegten Beginndatums wird das Enddatum berechnet
- auf der Grundlage des angegebenen Anfangsdatums werden die Umsetzungstermine auf der Grundlage der frühestmöglichen Termine festgelegt
- die Übergangszeit der Halbfabrikate, die nicht auf dem kritischen Pfad liegen, werden übernommen
- Rückwärts einstufig mit Kapazitätslimit
- ermöglicht die späteste Einlastung unter Berücksichtigung der Ressourcenkapazität (Einsatz und Buchung)
- Die Terminierung erfolgt auf der Grundlage der verfügbaren Ressourcenkapazität Mangelnde Materialverfügbarkeit hat keinen Einfluss auf die Terminierung
- das Beginndatum wird in Bezug auf das Beendigungsdatum berechnet.
- auf der Grundlage des angegebenen Beendigungsdatums werden die Umsetzungstermine auf der Grundlage der spätesten Termine festgelegt
Mehrstufige Einlastung hat folgende Variante:
- Vorwärts mehrstufig (mit oder ohne Kapazitätslimit)
- Rückwärts mehrstufig (mit oder ohne Kapazitätslimit)
- Vorwärts mehrstufig im Auftrag (mit oder ohne Kapazitätslimit)
- Rückwärts mehrstufig im Auftrag (mit oder ohne Kapazitätslimit)
Mehrstufige Einlastung
Mehrstufige Einlastung ermöglicht es, mehrstufige Produktionsstrukturen bei der Erstellung eines einzigen Produktionsauftrags herzustellen. Die folgenden Arten der mehrstufigen Einlastung können unterschieden werden:
- Mehrstufige Einlastung – sas System generiert zusätzliche Produktionsaufträge für die Halbfabrikate, die hergestellt werden, um den Anforderungen des zu erstellenden Produktionsauftrags gerecht zu werden. Sie zeichnet sich durch folgende Eigenschaften aus:
- das Beginn- und Enddatum für neue Produktionsaufträge für die Halbfabrikate werden entsprechend den Anforderungen des Hauptproduktionsauftrags festgelegt
- beim Erstellen nachfolgender Produktionsaufträge werden die in der Anwendung Artikel definierten Chargen- oder Planungsdaten nicht berücksichtigt
- um einen übergeordneten Produktionsauftrag neuzustarten, werden die bei der vorherigen Einlastung erstellten untergeordneten Aufträge gelöscht, und wenn keine Rückmeldung zu diesen Aufträgen vorliegt, werden neue Aufträge erstellt
- die erstellten untergeordneten Aufträge werden auf der Standardregisterkarte Belegkette angezeigt
- wenn die Aktion Einlasten und freigeben nicht ausgewählt ist, müssen die Aufträge separat freigegeben werden
- die Transportzeit wird berücksichtigt, bevor jeder nachfolgende Produktionsauftrag in Betrieb genommen wird
- die Übergangszeit-Lagerzugang wird nur am Ende des Hauptproduktionsauftrags berücksichtigt
- die Pufferzeiten werden immer berücksichtigt
- Mehrstufige Einlastung im Auftrag – das System plan die ganze Produktion in einem Produktionsauftrag Die Daten für die Halbfabrikate werden entnommen, indem sie in den Produktionsauftrag importiert werden. Sie zeichnet sich durch folgende Eigenschaften aus:
- Die Materialbuchungen und Ressorucenbuchungen werden für die ganze Produktiosnsstuktur erzeugt
- Die Transportzeit wird berücksichtigt, bevor der Arbeitsgang in Betrieb genommen wird
- Die Übergangszeit-Lagerzugang wird nur am Ende des Produktionsauftrags berücksichtigt
- Die Pufferzeiten werden immer berücksichtigt
Fristen
Die Einlastung ist mit der Festlegung der Beginn- und Beendigungszeiten eines Produktionsauftrags verbunden. Sie gelten als Basiszeit für die Berechnungen.
- Bei der Terminierung rückwärts wird der Beginn gemäß den Kapazitäten ab 24:00 Uhr am Vortag durchgeführt.
- Bei der Terminierung vorkwärts wird der Beginn gemäß den Kapazitäten ab 00:00 Uhr am aktuellen Tag durchgeführt.
Anfangs- und Beendigungsdaen werden abhängig von der Art der Planung und den Produktionsstrukturen für ein bestimmtes Produktionsprodukt unterschiedlich berücksichtigt oder berechnet:
- Das Standarddatum für das früheste Beginndatum ist immer das aktuelle Datum, d. h. heute
- Das Standarddatum für das späteste Enddatum ist das maximale Datum, d.h. der 31.12.9999
Die Berechnung von Beginn- und Endterminen unterscheidet sich je nach Erzeugung von Produktionsaufträgen für Produktionsartikel:
- die nur Stücklisten enthalten
- die eine Stückliste und einen Arbeitsplan bzw. einen Produktionsplan enthalten
Zeitberechnung für Produktionsartikel, die nur Stücklisten enthalten
Für Artikel, die nur eine Stückliste enthalten, werden die Produktionszeiten je nach der gewählten Terminierungsart berechnet.
- Terminierung Rückwärts mit einem bestimmten spätesten Beendigungsdatum:
- die Angabe des frühesten Beginntermins hat keinerlei Auswirkungen
- es wird die Länge des Produktionszyklus eines Artikels vom festgelegten spätesten Beendigungsdatum abgezogen und ergibt das aktuelle Beginndatum
- das aktuelle Beendigungsdatum stimmt mit dem festgelegten spätesten Beendigungsdatum überein
- Terminierung Rückwärts, das späteste Beendigungsdatum wird nicht definiert (d.h. im Feld Spätestes Ende ist das Datum 31.12.9999 definiert):
- es wird die Länge des Produktionszyklus eines Artikels vom festgelegten frühersten Beginndatum addiert und ergibt das aktuelle Beendigungsdatum
- das aktuelle Beginndatum stimmt mit dem festgelegten frühesten Beginndatum überein
- Terminierung Vorwärts:
- die Angabe des spätesten Beendigungsdatums hat keine Auswirkungen
- es wird die Länge des Produktionszyklus eines Artikels vom festgelegten frühersten Beginndatum addiert und ergibt das aktuelle Beendigungsdatum
- das aktuelle Beginndatum stimmt mit dem festgelegten frühesten Beginndatum überein
Zeitberechnung für Produktionsartikel, die nur Produktionsplan enthalten
- Terminierung Rückwärts mit einem bestimmten spätesten Beendigungsdatum:
- die Angabe des frühesten Beginntermins hat keinerlei Auswirkungen
- das aktuelle Beendigungsdatum stimmt mit dem festgelegten spätesten Beendigungsdatum überein
- das aktuelle Beginndatum wird auf der Grundlage des aktuellen Beendigungsdatums des Produktionsauftrags berechnet
- Terminierung Rückwärts, das späteste Beendigungsdatum wird nicht definiert (d.h. im Feld Spätestes Ende ist das Datum 31.12.9999 definiert):
- es wird die Länge des Produktionszyklus eines Artikels vom festgelegten frühersten Beginndatum addiert und ergibt das aktuelle Beendigungsdatum
- das aktuelle Beginndatum wird auf der Grundlage des aktuellen Datum der Freigabe des Produktionsauftrags berechnet
- Terminierung Vorwärts:
- die Angabe des spätesten Beendigungsdatums hat keine Auswirkungen
- das aktuelle Beginndatum stimmt mit dem festgelegten frühesten Beginndatum überein
- das aktuelle Beendigungsdatum wird auf der Grundlage des aktuellen Datum der Freigabe des Produktionsauftrags berechnet