Die Kommissionierung bezeichnet die Bereitstellung von Artikelbeständen für nachgelagerte Prozesse, z. B. im Vertrieb oder in der Produktion. Die Kommissionierung besteht in der Regel aus einer Umlagerung von einem Quell-Ort auf einen Ziel-Ort, an dem der Artikelbestand dem nachgelagerten Prozess zur Verfügung gestellt wird.
Die Grundlage der Kommissionierung bildet die Kommission. Sie fasst die benötigten Artikel in den korrekten Mengen und Ausprägungen zusammen. Ist der Lagerort in Lagerplätzen unterteilt, dann werden aus der Kommission heraus Lageraufträge erzeugt, die den Artikeltransport genau beschreiben.
Die Kommissionierung an unterteilten Lagerorten erfolgt innerhalb der Auslagerungslogik. Die Konfiguration der Lagerplatzsteuerung beeinflusst somit auch die Kommissionierung. Durch eine geeignete Konfiguration der Lagerplatzsteuerung können verschiedene Szenarien abgebildet werden, wie z. B. Kommissionierung über Kommissionierplatz oder über einen Kommissionierpunkt. Auch die Zusammenstellung der ausgelagerten Ware für die Kommissionen kann so eingestellt werden, dass verschiedene Szenarien abgebildet werden können, beispielsweise eine auftragsbezogene (einstufige) parallele Kommissionierung oder eine auftragsübergreifende (mehrstufige) Kommissionierung.
Dieses Dokument beschreibt die Kommissionierung an Lagerorten, die in Lagerplätzen unterteilt sind. Sie erfahren, welche Kommissionierungsszenarien mit Comarch ERP Enterprise möglich sind und welche Einstellmöglichkeiten dafür zur Verfügung stehen.
Einen Ablauf der Kommissionierung an einfachen Lagerorten sowie eine Beschreibung, wie die Kommission in die betriebswirtschaftlichen Prozesse eingebunden ist, finden Sie in der Dokumentation Kommissionen. Die bei der Kommissionierung verwendeten Anwendungen und deren Felder, Aktionen und Vorgehensweisen sind in separaten Dokumentationen ausführlich beschrieben.
Begriffsbestimmung
- Auslagerrestriktionen – Die Auslagerrestriktion bezeichnet und umfasst Bedingungen für die Auslagerung von Artikeln, die auf Lagerplätzen lagern. Mithilfe der Auslagerrestriktion kann beispielsweise die Reihenfolge festgelegt werden, in der die einzelnen Lagerzonen bei der Auslagerung zu berücksichtigen sind. Auch der Ein- oder Ausschluss von bestimmten Lagereinheiten kann als Restriktion für die Auslagerung bestimmt werden.
- Ausprägungen – Eine Ausprägung identifiziert einen konkreten Artikel. So wird z. B. ein Fernseher neben der Artikelnummer auch durch die Ausprägung Seriennummer identifiziert und damit einmalig. Unterstützt werden die Ausprägungen Charge, Los und Seriennummer.
- Kommissionierplatz – Der Kommissionierplatz ist ein Lagerplatz der Verwendung Kommissionierung dient der zwischenzeitlichen Lagerung von Artikeln für den Versand. Durch die Verwendung von Kommissionierplätzen kann die Zeit für das Bereitstellen von Artikeln für Kundenlieferungen verkürzt werden.
- Kommissionierstrategien – Die Kommissionierstrategie steuert, wie eine Auslagerung erfolgt, wenn in der Lagerzone kein fixer Kommissionierplatz für den auszulagernden Artikel vorhanden ist oder der Bestand auf einem vorhandenen Kommissionierplatz nicht ausreichend ist. In diesem Fall erfolgt die Auslagerung von einem Reserveplatz entweder über die Warenausgangszone (Kommissionierpunkt) oder direkt vom Lagerplatz (Fachkommissionierung).
- Kommissionierungen – Die Kommissionierung ist ein manuelles oder automatisiertes Entnehmen und Zusammenstellen von bestimmten Mengen der Artikel aus dem Lager. Die Grundlage bildet die Kommission, die nach den Bedarfsinformationen des Vertriebs oder der Produktion erstellt wird.
- Nachschubauftrag – Nachschubaufträge dienen dem Auffüllen von Kommissionierplätzen: Bei jeder Abgangsbuchung vom Kommissionierplatz wird der neue Bestand mit einem Meldebestand verglichen. Wenn der neue Bestand kleiner ist als der Meldebestand, dann kann ein Nachschubauftrag automatisch erzeugt werden, der den Füllbestand laut Nachschubdefinition wieder herstellt.
Prozessschritte
Die folgende Abbildung gibt einen Überblick über die Kommissionierung an einem unterteilten Lagerort. Dabei ist unerheblich, ob die Kommission aus dem Vertrieb, der Produktion oder der Beschaffung entstanden ist; die Prozessschritte sind stets gleich.
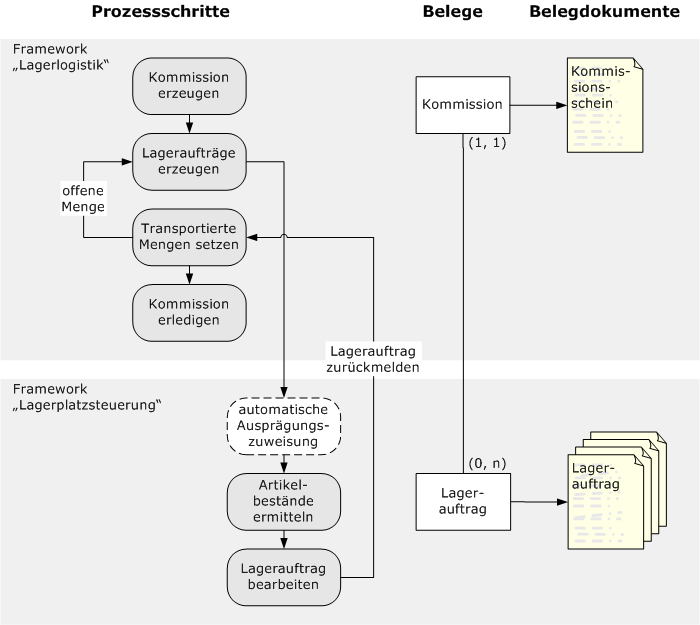
Aus der Kommission heraus werden Transportanweisungen in Form von Lageraufträgen entweder automatisch oder manuell erzeugt. Durch die Rückmeldung werden die kommissionierten Mengen in der Kommission gesetzt. Kann eine Teilmenge nicht bedient werden, kann diese im Lagerauftrag ohne Rückmeldung erledigt werden. Sind alle Lageraufträge erledigt, die Mengen jedoch nicht in voller Höhe zurückgemeldet, können weitere Lageraufträge für die noch offenen Mengen in der Kommission erzeugt werden. Auch kann über den Lagerauftrag eine größere Menge zurückgemeldet werden, als für die Kommissionierung benötigt wird.
Um eine Kommission zu erledigen oder zu stornieren, müssen alle erzeugten Lageraufträge entweder zurückgemeldet oder ohne Rückmeldung erledigt sein.
Wird ein in Ausprägungen geführter Artikel kommissioniert und sind die konkreten Ausprägungen noch nicht bekannt, dann findet spätestens mit dem Erzeugen der Lageraufträge die automatische Ausprägungszuweisung statt. Eine Beschreibung der Ausprägungszuweisung finden Sie in der Dokumentation Ausprägungszuweisung.
Ablauf der Kommissionierung
Bei einer Kommissionierung an unterteilten Lagerorten werden im Prinzip zwei Schritte durchlaufen:
- Die zu kommissionierende Ware wird mithilfe der Auslagerungslogik automatisch ausgelagert.
- Die ausgelagerte Ware wird für die Kommissionen zusammengestellt.
Nachfolgend werden die verschiedenen Möglichkeiten des Kommissionierungsablaufs erläutert. Zunächst wird die Kommissionierung in Bezug auf die Auslagerung der Ware betrachtet, anschließend in Bezug auf die Zusammenstellung der Ware (siehe Abschnitt Zusammenstellung der Ware).
Automatische Auslagerung der Ware
Auslagerungsszenarien
Kommissionierung über den Kommissionierplatz
Enthält die Lagerzone einen fixen Kommissionierplatz, dann sind die Fachkommissionierung sowie die Auslagerung über den Kommissionierpunkt nicht zulässig. Eventuelle Restmengen werden stattdessen dem fixen Kommissionierplatz entnommen. In diesem Falle ermittelt die Auslagerungslogik nur artikel- und ausprägungsreine Reserveplätze, deren Artikelbestand kleiner oder gleich dem Restbestand ist. Dadurch werden keine Rücklagerungsaufträge erzeugt, wenn in der Lagerzone ein fixer Kommissionierplatz vorhanden ist.
Die folgende Abbildung zeigt die Kommissionierung von 14 Lagereinheiten für den Vertrieb. Der Lagerort besteht aus einer gemischten Lagerzone mit Reserveplätzen und einem fixen Kommissionierplatz für den Artikel. Anbruchsmengen werden bevorzugt ausgelagert. Der kommissionierte Bestand ist in blauer Farbe dargestellt. Bestände, die nicht kommissioniert werden, sind mit grauer Farbe gekennzeichnet.
Zunächst werden die beiden angebrochenen Lademittel von den Reserveplätzen in die Warenausgangszone umgelagert. Anschließend wird ein ganzes Lademittel umgelagert. Die Restmenge von 3 Lagereinheiten wird dem Kommissionierplatz entnommen.
Ein ausreichender Bestand auf den Kommissionierplätzen ist die Voraussetzung für eine reibungslose Kommissionierung. Weitere Informationen dazu finden Sie im Abschnitt Auffüllen von Kommissionierplätzen.
Kommissionierung über den Kommissionierpunkt
Ist in der Lagerzone kein fixer Kommissionierplatz vorhanden, dann erfolgt bei der Kommissionierstrategie Kommissionierpunkt die Kommissionierung in der Warenausgangszone. Ist die transportierte Menge größer als die angeforderte Menge, erfolgt anschließend eine Rücklagerung von der Warenausgangszone zurück auf den Quell-Platz.
Die folgende Abbildung zeigt die Kommissionierung von 2 Lagereinheiten für den Vertrieb. Der Lagerort besteht aus einer Reservezone mit artikelreinen Lademitteln. Kommissionierplätze sind nicht vorhanden. Der kommissionierte Bestand ist in blauer Farbe dargestellt. Bestände, die nicht kommissioniert werden, sind mit grauer Farbe gekennzeichnet. Die Rücklagerung ist in grüner Farbe dargestellt.
Zunächst wird ein ganzes Lademittel mit 6 Lagereinheiten in die Warenausgangszone umgelagert. Dort findet die Kommissionierung von 2 Lagereinheiten statt. Anschließend wird die Restmenge von 4 Lagereinheiten auf den Quell-Platz zurückgelagert.
Ist ein Artikel in Chargen oder Losen geführt und befinden sich auf einem Lagerplatz unterschiedliche Ausprägungen von dem Artikel, dann werden Transportanweisungen nur über die Ausprägungen erstellt, die wirklich ausgelagert werden. Bestandsänderungen werden ohne Lademittel durchgeführt. Im Lagerauftrag wird allerdings die Angabe Mit Lademittel gemacht, um zu kennzeichnen, dass trotzdem der gesamte Bestand auf dem Lademittel zum Kommissionierpunkt transportiert wird. Restmengen der zu kommissionierenden einzelnen Ausprägungen werden auch zurückgelagert.
Ist der Artikel in Seriennummern geführt und wurden unterschiedliche Seriennummern in die Warenausgangszone umgelagert, dann ist zum Zeitpunkt der Erzeugung des Lagerauftrages für die Rücklagerung nicht bekannt, welche davon später zurückgelagert werden. Daher wird bei seriennummergeführten Artikeln (mit oder ohne Bestandsführung) immer die Kommissionierstrategie Beliebiger Lagerplatz verwendet.
Lagern auf einem artikelunreinen Lademittel verschiedene Artikel, dann wird bei der Kommissionierstrategie Kommissionierpunkt nur der Bestand von dem zu kommissionierenden Artikel in die Warenausgangszone umgelagert. Die folgende Abbildung zeigt die Kommissionierung von 2 Lagereinheiten für den Vertrieb. Auf dem Lademittel sind 4 Lagereinheiten vom angeforderten Artikel und 2 Lagereinheiten von einem anderen Artikel (rote Kreise) vorhanden.
Die Umlagerung von 4 Lagereinheiten in die Warenausgangszone sowie die Rücklagerung auf den Quell-Platz erfolgen in diesem Falle ohne Lademittel. Durch die Rücklagerung entsteht ein künftiger Zugang am Quell-Platz. Daher werden die Bestände auf dem Lademittel solange für die Kommissionierung nicht berücksichtigt, bis die Rücklagerung zurückgemeldet oder ohne Rückmeldung erledigt wurde.
Kommissionierung über den Quell-Platz (Fachkommissionierung)
Ist in der Lagerzone kein fixer Kommissionierplatz vorhanden, dann erfolgt bei der Kommissionierstrategie Beliebiger Lagerplatz die Kommissionierung per Fachkommissionierung direkt am Quell-Platz.
Die folgende Abbildung zeigt die Kommissionierung von 2 Lagereinheiten für den Vertrieb. Der Lagerort besteht aus einer Reservezone. Kommissionierplätze sind nicht vorhanden. Der kommissionierte Bestand ist in blauer Farbe dargestellt. Bestände, die nicht kommissioniert werden, sind mit grauer Farbe gekennzeichnet.
Der zu kommissionierende Bestand von 2 St. wird vom Quell-Platz in die Warenausgangszone umgelagert.
Kommissionierung bei mehreren Lagerzonen
Aus Sicht der Kommissionierung dient die Auslagerrestriktion vor allem der Festlegung der Reihenfolge, in der die einzelnen Lagerzonen bei der Auslagerung berücksichtigt werden. In den beiden folgenden Kapiteln wird die Kommissionierung an einem Lagerort mit zwei Lagerzonen beispielhaft dargestellt. Im ersten Kapitel wird die Reservezone vor der Kommissionierzone berücksichtigt. Im zweiten Beispiel ist die Reihenfolge in der Auslagerrestriktion umgekehrt.
Reservezone vor Kommissionierzone
Die folgende Abbildung zeigt die Kommissionierung von 9 Lagereinheiten für den Vertrieb. Der Lagerort besteht aus einer Reservezone und einer Kommissionierzone mit einem fixen Kommissionierplatz für den Artikel. In der Auslagerrestriktion hat die Reservezone Vorrang vor der Kommissionierzone. Für die Reservezone wird die Kommissionierstrategie Beliebiger Lagerplatz verwendet. Der kommissionierte Bestand ist in blauer Farbe dargestellt. Bestände, die nicht kommissioniert werden, sind mit grauer Farbe gekennzeichnet.
Zunächst wird ein ganzes Lademittel mit 6 Lagereinheiten vom Quell-Platz in die Warenausgangszone umgelagert. Die Restmenge von 3 Lagereinheiten wird per Fachkommission dem Quell-Platz direkt entnommen und ebenfalls in die Warenausgangszone umgelagert.
Ist in der Auslagerrestriktion für die Reservezone der Wert Nur ganze Lademittel hinterlegt, dann ist weder eine Fachkommissionierung noch eine Rücklagerung zulässig. Angenommen ein Lademittel mit genau dem angeforderten Bestand befindet sich in der Reservezone, dann kann die Kommissionierung trotzdem von der Reservezone erfolgen, wie die folgende Abbildung zeigt.
Ist in der Auslagerrestriktion nur diejenige Einheit eingeschlossen, die einem vollen Lademittel entspricht (hier: Pal), dann wird die Restmenge vom Kommissionierplatz der Kommissionierzone genommen, wie die folgende Abbildung zeigt.
Kommissionierzone vor Reservezone
Die folgende Abbildung zeigt die Kommissionierung von einem vollen Lademittel für den Vertrieb. Der Lagerort besteht aus einer Reservezone und einer Kommissionierzone mit einem fixen Kommissionierplatz für den Artikel. In der Auslagerrestriktion hat die Kommissionierzone Vorrang vor der Reservezone. Der kommissionierte Bestand ist in blauer Farbe dargestellt. Bestände, die nicht kommissioniert werden, sind mit grauer Farbe gekennzeichnet.
Auch wenn der zu kommissionierende Bestand genau einem vollen Lademittel entspricht, wird der Bestand vom Kommissionierplatz und nicht von der Reservezone genommen.
Ist der zu kommissionierende Bestand größer als der aktuelle Bestand auf dem Kommissionierplatz, dann wird nur der auf dem Kommissionierplatz verfügbare Bestand umgelagert. Die folgende Abbildung zeigt die Kommissionierung von 16 Lagereinheiten für den Vertrieb.
Zunächst wird der aktuelle Bestand von 8 Lagereinheiten vom Kommissionierplatz in die Warenausgangszone umgelagert. Anschließend werden 8 Lagereinheiten aus zwei Lagerplätzen in der Reservezone in die Warenausgangszone umgelagert.
Auslagerung von Set-Artikeln (Sonderfall)
Wird in einem Vertriebsauftrag eine Grundposition mit einem Set-Artikel erfasst, dann werden die Komponenten der entsprechenden Handelsstückliste als Detailpositionen dargestellt. Beim Erzeugen einer Kommission werden diese Positionen als Grund- und Detail-Kommissionspositionen übernommen.
Für die Auslagerung werden die Mengen von Detail-Kommissionspositionen benutzt. Sind die gesamten Komponentenmengen auslagerbar, dann kann die gesamte Anzahl von Sets kommissioniert werden.
Wenn allerdings nicht alle Mengen von Komponenten ausgelagert werden können, dann wird die zu kommissionierende Menge des Set-Artikels so reduziert, dass die Auslagerung von allen Komponentenmengen gleichzeitig erfolgen kann. Die Menge des Set-Artikels bleibt dabei ganzzahlig.
Das folgende Beispiel zeigt den Entscheidungsweg bei der Auslagerung von einem Set-Artikel in einer konkreten Bestandssituation.
- 7 Stk von dem Artikel A1
- 4 kg von dem Artikel A2
Es sollen 10 Stk von dem Set-Artikel auf einem Lagerort L kommissioniert werden.
Verfügbare Bestände der Artikel A1 und A2 auf dem Lagerort L sehen wie folgt aus:
- 60 Stk von dem Artikel A1 liegen auf einer gemischten Lagerzone auf Reserve-Plätzen je 10 Stk pro volles Lademittel; der Kommissionierplatz für den Artikel A1 in der gleichen Zone hat den Bestand 2 Stk.
- 40 kg von dem Artikel A2 sind auf einem Kommissionierplatz eingelagert.
Die Detailpositionen in der Kommission haben die Mengen 70 Stk von dem Artikel A1 und 40 kg von dem Artikel A2.
Es werden folgende auslagerbare Mengen ermittelt:
- Maximal 62 Stk von dem Artikel A1
- Maximal 40 kg von dem Artikel A2
Daraus resultiert, dass anstatt 10 nur 8 Sets ausgelagert werden können, und die zu kommissionierenden Mengen würden betragen:
- 8 x 7 Stk = 56 Stk von dem Artikel A1
- 8 x 4 kg = 32 kg von dem Artikel A2
Da allerdings in einer gemischten Zone von Reserve-Plätzen nur ganze Lademittel ausgelagert werden können, können nicht die gesamten 56 Stk sondern nur 52 Stk (5 Lademittel je 10 Stk + 2 Stk von dem Kommissionierplatz) kommissioniert werden, was nach sich zieht, dass nicht 8 sondern maximal 7 Sets nach den Regeln der Lagerplatzsteuerung kommissionierbar wären. Dies ergibt folgende Mengen:
- 7 x 7 Stk = 49 Stk von dem Artikel A1
- 7 x 4 kg = 28 kg von dem Artikel A2
Wegen der gleichen Regeln wie oben können die 49 Stk von dem Artikel A1 auf dem Lagerort L nicht ausgelagert werden; mögliche Mengen betrügen
- Maximal 42 Stk von dem Artikel A1
- Maximal 28 kg von dem Artikel A2
Diese Werte beschränken die Anzahl von kommissionierbaren Sets auf 6 mit folgenden auszulagernden Mengen:
- 6 x 7 Stk = 42 Stk von dem Artikel A1
- 6 x 4 kg = 24 kg von dem Artikel A2
Es werden also Lagerauftragspositionen für die Auslagerung von 42 Stk des Artikels A1 (4 Lademittel je 10 Stk + 2 Stk von dem Kommissionierplatz) und 24 kg des Artikels A2 erzeugt.
Einstellungen für die automatische Auslagerung
Die Kommissionierung erfolgt innerhalb der Auslagerungslogik. Die Konfiguration der Lagerplatzsteuerung beeinflusst somit auch die Kommissionierung. Im Folgenden werden einige für die Kommissionierung relevanten Größen erläutert. Eine Beschreibung der Auslagerungslogik finden Sie in der Dokumentation Einführung: Lagerplatzsteuerung.
- Auslagerrestriktionen – Mithilfe der Auslagerrestriktion können Sie die Reihenfolge festlegen, in der die einzelnen Lagerzonen eines Lagerortes berücksichtigt werden. Mithilfe der Auslagerrestriktion können Sie z. B. festlegen, ob eine eventuelle Kommissionierzone vor oder nach den Lagerzonen mit Reserveplätzen berücksichtigt wird.
Bei der Auslagerstrategie Strenges FIFO werden die Artikelbestände strikt nach ihrem FIFO-Datum ausgelagert. Daher berücksichtigt die Auslagerungslogik weder die Auslagerrestriktionen noch Artikelbestände auf Kommissionierplätzen.
In der Dokumentation Auslagerrestriktionen finden Sie eine ausführliche Beschreibung der Auslagerrestriktionen. - Kommissionierstrategien – Die Kommissionierstrategie entscheidet darüber, wie die Kommissionierung erfolgt, wenn in der Lagerzone kein fixer Kommissionierplatz vorhanden ist. Bei der Kommissionierstrategie Beliebiger Lagerplatz wird die zu kommissionierende Menge dem Artikelbestand am Quell-Platz entnommen. Bei der Kommissionierstrategie Kommissionierpunkt wird der Artikelbestand zuerst in die Warenausgangszone (Kommissionierpunkt) transportiert. Ein eventueller Restbestand wird anschließend auf den Quell-Platz zurückgelagert.
In der Dokumentation Einführung: Lagerstrategien finden Sie eine ausführliche Beschreibung der Kommissionierstrategien. Die Dokumentation Einführung: Transportvorgänge enthält eine Beschreibung der unter Verwendung der möglichen Kommissionierstrategien erzeugten Lageraufträge. - Kommissionierzonen – Die Kommissionierzone ist eine Lagerzone der Verwendung Kommissionierung. In einer Kommissionierzone können nur Kommissionierplätze erfasst werden. Ein unterteilter Lagerort kann beliebig viele Kommissionierzonen enthalten.HinweisAuch wenn die Kommissionierzone als einfache Lagerzone ohne Lagerplätze erfasst werden kann, ist diese Lagerorganisation für eine Kommissionierzone nicht geeignet, da sie keine Kommissionierplätze zulässt.
- Kommissionierplätze – Ein Kommissionierplatz ist ein Lagerplatz der Lagerplatzart Kommissionierplatz ohne Lademittel. Wie die Lagerplatzart besagt, sind auf dem Kommissionierplatz keine Lademittel zulässig. Kommissionierplätze können sowohl für Kommissionierzonen als auch für Lagerzonen der Verwendung Keine Angabe erfasst werden.
Ist bei einem Kommissionierplatz eine Nachschubdefinition für einen Artikel hinterlegt, dann ist dieser Artikel dem Kommissionierplatz fest zugeordnet. Ein solcher Kommissionierplatz wird daher auch fixer Kommissionierplatz für den Artikel genannt. Ein Artikel kann beliebig viele fixe Kommissionierplätze pro Lagerzone haben.
Der Kommissionierplatz gilt immer als nutzbar unabhängig von den Einstellungen der Checkbox Nutzbar der Anwendung Lagerplätze. - Nachschubdefinitionen – Die Nachschubdefinition dient dem automatischen Auffüllen von fixen Kommissionierplätzen. Ein Artikel, der in Seriennummern mit Bestandsführung geführt wird, kann keine Nachschubdefinition haben.
Zusammenstellung der Ware
Kommissionierungsszenarien
Die Zusammenstellung der Ware innerhalb der Kommissionierung kann auf unterschiedliche Art organisiert werden. Im Allgemeinen wird zwischen einstufiger und mehrstufiger Kommissionierung unterschieden. Während bei der einstufigen Kommissionierung jeder Auftrag einzeln kommissioniert wird, kann bei der mehrstufigen Kommissionierung die Ware für mehrere Aufträge gleichzeitig zusammengestellt werden. Im Folgenden wird daher zwischen auftragsbezogener und auftragsübergreifender Kommissionierung unterschieden.
Auftragsbezogene (einstufige) Kommissionierung
Die Lageraufträge werden ausgehend von nur einer Kommission erzeugt. Dabei wird für jeden Lagerort mindestens ein Lagerauftrag und ggf. ein Rücklagerauftrag erzeugt. Für die Abarbeitung der Lageraufträge durch die Kommissionierer bestehen folgende Möglichkeiten:
- Serielle auftragsbezogene Kommissionierung – Pro Kommissioniervorgang wird ein Lagerauftrag erzeugt, der von einem Kommissionierer abgearbeitet wird.
- Parallele auftragsbezogene Kommissionierung – Pro Kommissioniervorgang werden mehrere Lageraufträge erzeugt, die von mehreren Kommissionierern parallel abgearbeitet werden können. Dazu können Merkmale angegeben werden, anhand derer die Positionen automatisch zu Lageraufträgen gruppiert werden, beispielsweise nach Lagergängen.
Auch die Sortierung der Lagerauftragspositionen kann festgelegt werden.
Auftragsübergreifende (mehrstufige) Kommissionierung
Die Lageraufträge werden ausgehend von mehreren Kommissionen erzeugt. Mithilfe von Lageranforderungen werden die Kommissionspositionen zunächst automatisch gruppiert. Dabei werden die Kommissionspositionen mit demselben Bestandseigentümer, Lagerort und Artikel automatisch in einer Lageranforderungsposition zusammengefasst. Anschließend werden aus den Lageranforderungen automatisch Lageraufträge erzeugt.
Darüber hinaus werden bei einer artikelbezogenen auftragsübergreifenden Kommissionierung die Lageranforderungspositionen, die denselben Artikel enthalten, in einem Lagerauftrag zusammengefasst.
Einstellungen für die Zusammenstellung der Ware
Im Folgenden werden die Einflussfaktoren genannt, die für die Zusammenstellung der Ware im Kommissionierungsprozess relevant sind. Eine detaillierte Beschreibung der Einstellmöglichkeiten finden Sie in der Dokumentation der betreffenden Anwendungen.
- Festlegung der auftragsbezogenen oder auftragsübergreifenden Kommissionierung für Artikel in der Anwendung Artikel, Ansicht Lagerlogistik
- Gruppier- und Sortiermerkmale für die Lagerauftragserzeugung in den Anwendungen Lagerorte und Lager-Auftragsarten
- Verwendung von Lageranforderungen vom Typ Entnahme für Kommission in der Anwendung Kommissionsarten
- Kommissionierstrategie Kommissionierung ohne Rücklagerung in der Anwendung Lagerstrategien
Stornierung einer Kommission
Eine Kommission kann nur dann storniert werden, wenn keine offenen Lageraufträge existieren. Wurden aus der Kommission heraus erzeugte Lageraufträge bereits zurückgemeldet, dann müssen Artikelbestände, die sich in der Warenausgangszone befinden, unter Umständen rückgelagert werden. Die Rücklagerung erfolgt nicht automatisch, kann aber mithilfe einer Lageranforderung oder manueller Materialbuchung abgebildet werden.
Auffüllen von Kommissionierplätzen
Ein ausreichender Bestand auf den Kommissionierplätzen ist die Voraussetzung für eine reibungslose Kommissionierung. Daher müssen die Kommissionierplätze bei Bedarf wieder aufgefüllt werden. Im Folgenden werden die verschiedenen Möglichkeiten zum Auffüllen der Kommissionierplätze erläutert.
Durch die Einlagerungslogik
Die Einlagerungslogik stellt den Füllbestand auf fixen Kommissionierplätzen am Lagerort wieder her, wenn die folgenden Bedingungen erfüllt sind:
- Der aktuelle Bestand auf dem Kommissionierplatz ist kleiner als der Meldebestand in der Nachschubdefinition.
- Für den Kommissionierplatz existieren keine künftigen Zugänge. Insbesondere dürfen keine offenen Nachschubaufträge für den Kommissionierplatz vorhanden sein.
- Die Lagerzone, in der sich der Kommissionierplatz befindet, wird von der Einlagerungslogik berücksichtigt. Ein Ausschluss kann z. B. durch die Einlagerrestriktion gegeben sein.
Somit kann z. B. das Buchen eines Wareneinganges in eine Umlagerung von der Wareneingangszone direkt auf einen Kommissionierplatz resultieren.
Kommissionierplätze können auch durch die Auffüllstrategie Alle Plätze aufgefüllt werden. In diesem Fall werden die Kommissionierplätze nicht bis zum Füllbestand, sondern bis zum Maximalbestand laut Nachschubdefinition aufgefüllt.
Automatisch erzeugte Nachschubaufträge
Ein Nachschubauftrag ist ein Lagerauftrag vom Transportvorgang Umlagerung, der nicht durch einen Beleg, wie z. B. die Kommission, sondern durch die Unterschreitung des Meldebestandes auf einem Kommissionierplatz erzeugt wird. Somit hat ein Nachschubauftrag keinen Vorgänger in der Belegkette. Ansonsten unterscheidet er sich nicht von einem gewöhnlichen Lagerauftrag und kann anschließend genauso ausgegeben, zurückgemeldet oder ohne Rückmeldung erledigt werden. Die Lagerauftragsart von Nachschubaufträgen wird in der Anwendung Customizing hinterlegt.
Mit dem Nachschubauftrag wird versucht, den Füllbestand durch eine Umlagerung innerhalb des Lagerortes zu erreichen. Ein Nachschubauftrag wird auch dann erzeugt, wenn der ermittelte Artikelbestand nicht ausreicht, um den Füllbestand zu erreichen. Die Umlagerung erfolgt nicht über die Warenausgangszone sondern direkt auf den Kommissionierplatz. Um die passenden Artikelbestände zu ermitteln, wird die Auslagerungslogik verwendet. Ist in der Nachschubdefinition eine Lagerzone hinterlegt, dann wird die Ermittlung auf diese Lagerzone beschränkt, auch dann, wenn diese Lagerzone durch eine Auslagerrestriktion ausgeschlossen ist. Kommissionierplätze sind als Quell-Plätze für den Nachschubauftrag ausgeschlossen, auch dann, wenn sie sich in einer anderen Lagerzone befinden.
Das System gibt keine Meldung aus, wenn der Nachschubauftrag nicht erzeuget werden kann. Ein Nicht-Auffüllen kann z. B. die folgenden Ursachen haben:
- In der Nachschubdefinition wurde keine Füllmenge angegeben.
- Die Auslagerungslogik kann keinen Bestand ermitteln.
- Für den Kommissionierplatz existieren zukünftige Zugänge, z. B. durch einen erzeugten aber noch nicht zurückgemeldeten Nachschubauftrag.
- Der Kommissionierplatz befindet sich in einer Lagerzone mit dem Qualitätssicherungs-Status Quarantäne oder Gesperrt.
- In der Anwendung Customizing wurde keine Lagerauftragsart für die Nachschubaufträge hinterlegt.
Entsteht beim Erzeugen des Nachschubauftrages ein fehlerhafter Zustand im Lagerlogistik-Server, dann erfolgt die Kommissionierung nicht vom Kommissionierplatz, sondern von der Inventurdifferenz-Zone. Dies kann z. B. der Fall sein, wenn in der Nachschubdefinition eine ungültige Nachschublosgröße angegeben wurde.
Ist die umgelagerte Bestandsmenge größer als die benötigte Bestandsmenge, um den Füllbestand zu erreichen, dann erfolgt eine Rücklagerung vom Kommissionierplatz zurück auf den Quell-Platz. Dies kann z. B. dann der Fall sein, wenn die Kommissionierstrategie Kommissionierpunkt verwendet wird, oder der Nachschub laut Nachschubdefinition in einer bestimmten Losgröße erfolgt. Eine Rücklagerung erfolgt auch dann, wenn durch die Umlagerung der Maximalbestand am Kommissionierplatz nicht überschritten wurde. Wird der Rücklagerungsauftrag ohne Rückmeldung erledigt, dann bleibt der umgelagerte Bestand auf dem Kommissionierplatz und kann für künftige Kommissionierungen verwendet werden.
Beim Auffüllen von Kommissionierplätzen mit einem in Chargen (oder in Losen) geführten Artikel ermittelt die Auslagerungslogik in der Regel die älteste noch nicht abgelaufene Charge. Wenn eine jüngere Charge kommissioniert werden soll, kann es daher vorkommen, dass auf dem Kommissionierplatz ein ausreichender Bestand vom Artikel vorhanden ist und die Charge sich noch auf einem Reserveplatz befindet. In diesem Falle muss unter Umständen zuerst die angeforderte Charge mithilfe einer Lageranforderung auf den Kommissionierplatz umgelagert werden, bevor die Kommission erfolgen kann. Wird der aus der Kommission heraus erzeugte Lagerauftrag vor der Umlagerung zurückgemeldet, dann bleibt der Bestand der Charge auf dem Kommissionierplatz so lange negativ, bis die Umlagerung zurückgemeldet wird.
Manuelles Auffüllen
Kommissionierplätze können auch mithilfe der Anwendungen Materialbuchungen und Lageranforderungen manuell aufgefüllt werden. Wird ein Kommissionierplatz als Ziel-Platz in einer Lageranforderung vom Typ Umlagerung angegeben, dann berücksichtigt die Auslagerungslogik keine Bestände auf Kommissionierplätzen, da sonst eine Umlagerung von Kommissionierplatz auf Kommissionierplatz erfolgen könnte.
Beim Auffüllen von Kommissionierplätzen mit einem in Chargen (oder in Losen) geführten Artikel ohne Angabe eines Quell-Platzes in der Lageranforderung können zwei Lageraufträge erzeugt werden. Der erste Lagerauftrag lagert den Artikelbestand in die Wareneingangszone um. Für jede ermittelte Charge wird eine Lagerauftragsposition erzeugt. Der zweite Lagerauftrag lagert den Artikelbestand von der Wareneingangszone auf den Kommissionierplatz um. Beim Erzeugen des zweiten Lagerauftrages sind die durch die Auslagerungslogik ermittelten Chargen jedoch nicht bekannt. Somit umfasst der zweite Lagerauftrag nur eine einzige Position ohne Angabe einer konkreten Charge. Da dem Lagerauftrag weder Positionen noch Chargen hinzugefügt werden können, kann im zweiten Lagerauftrag nur eine einzige Charge auf den Kommissionierplatz umgelagert werden. Die restlichen Chargen können z. B. mithilfe weiterer Lageranforderungen oder manueller Materialbuchungen auf den Kommissionierplatz umgelagert werden.