Das Modul Produktion im Comarch ERP Enterprise System ermöglicht es, die Produktionstätigkeit eines Unternehmens mit Unterstützung von Produktionsprozessen zu steuern. Das Modul Produktion ist in die folgenden Elemente unterteilt:
- Produktionsstrukturen – ermöglichen die Definition des gesamten Produktionsprozesses. Die Produktionsstrukturen sind: Arbeitsgänge, Arbeitspläne, Produktionsplan, Stücklisten.
- Ressourcen – ermöglichen die Einführung und Verwaltung der Ressourcen eines bestimmten Unternehmens im Laufe der Zeit. Im System können Ressourcen als eine einzelne Ressource, eine Ressourcengruppe oder eine -Liste definiert werden.
- Produktionsorganisation – Zeitmanagement und Dokumentationserstellung. Für die Verwaltung von Produktionsdaten sind auch Prozesse erforderlich, die von Hintergrund-Anwendungen unterstützt werden.
- Produktionsauftrag – die wichtigste Anwendung des Moduls Produktion, die für die Durchführung der Produktion im System verantwortlich ist.
- Buchungen– eine Reihe von Anwendungen, die die Arbeitsgangbuchungen ermöglichen.
- Fremdfertigung – ermöglicht die Integration der Produktionsvorgänge, die außerhalb des Unternehmens durchgeführt werden.
- Produktkonfiguration – für die Herstellung verschiedener Produktvarianten ermöglicht das System die Erstellung eines Produkt-Konfigurators.
- Berechnung der Produktions-Bestandswerte – diese Funktion ermöglicht die Bewertung von Materialien, die in den gestarteten Produktionsprozessen verwendet werden.
- Zusatzfunktionen des Produktionsmoduls – ermöglichen die Anpassung der Produktionsstrukturen an den ausgewählten Produktionsartikel.
Das Produktionsmodul kann mit anderen Bereichen des Systems interagieren, wie z. B.:
- Disposition
- Kalkulation
- Vertrieb
- Lagerlogistik
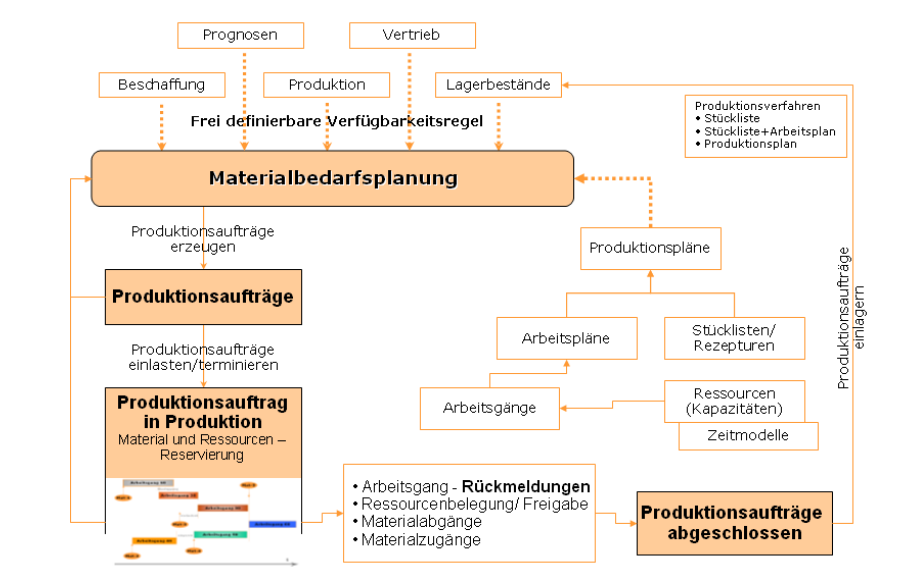
Das Diagramm zeigt die Verknüpfungen in der Produktion. Es zeigt die Kooperation zwischen den grundlegenden Produktionsdaten und dem Produktionsprozess sowie die Faktoren, die die Produktion beeinflussen. Ein Beispiel dafür, wie man einen Produktionsprozess im ERP-System Schritt für Schritt definieren kann finden Sie in dem Artikel Beispiel für die Konfiguration eines Produktionsprozesses im ERP-System.
Produktionsstrukturen
Mit Produktionsstrukturen können Sie die für den Produktionsprozess notwendigen Daten zu definieren. Das System ermöglicht die Durchführung von Produktionsprozessen auf Basis von Produktionsdaten, die einem Produktionsartikel in der Anwendung Artikel → Ansicht Produktion zugeordnet werden, das sind:
- Stücklisten – nur Materialien werden für die Produktion entnommen, Produktionsaufträge werden zeitlich nicht eingeplant
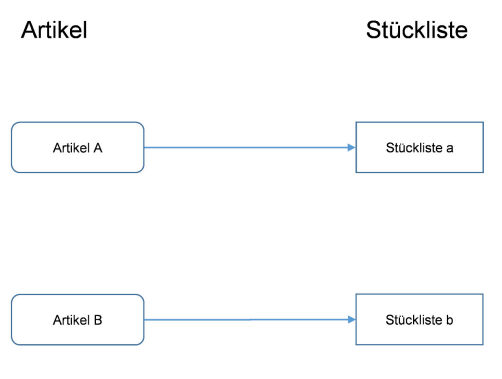
- Stücklisten und Arbeitspläne – Materialien werden anhand der zugewiesenen Stückliste in die Produktion entnommen und Vorgänge anhand des zugewiesenen Arbeitsplans geplant
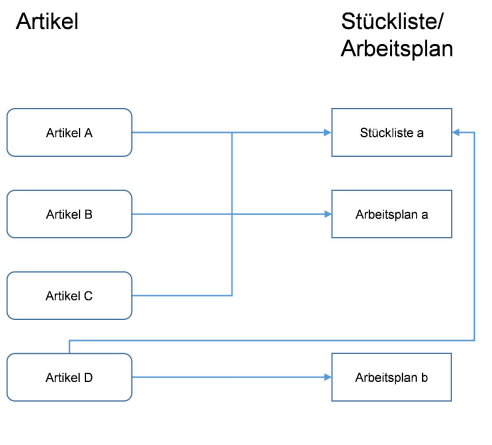
- Produktionsplan – für die Produktion werden Materialien entnommen, die je nach dem definierten Produktionsplan zugeordnet werden
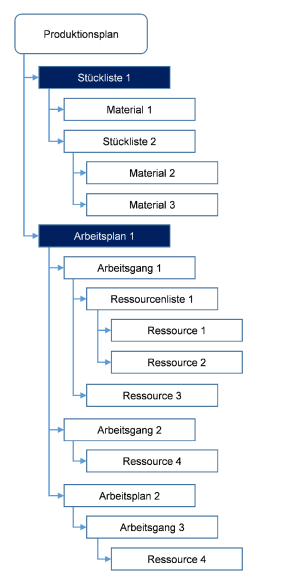
Die Mindestanforderung an einen Produktionsprozess ist die Erstellung einer Stückliste, die mindestens ein Material enthält, und dessen Zuordnung zu einem Produktionsartikel. Dies ermöglicht einen reinen Materialbetrieb. Es ist nicht notwendig, zeitdefinierte Daten (Ressourcen, Vorgänge und Arbeitspläne) zu definieren und zu verwenden.
Die Produktionsstrukturen im System sind:
- Stückliste – systematische Zusammenstellungen aller Bestandteile zur Produktion von Artikeln. Sie können Rohstoffe, Materialien, Halbfabrikate oder weitere Stücklisten enthalten. Den Produktions-Artikeln können eine oder mehrere Stücklisten (über Produktionsverfahren) zugeordnet werden.
- Arbeitsgang – eine Tätigkeit, die im Produktionsprozess ausgeführt wird. Dem Arbeitsgang werden Ressourcen zugeordnet, die für die Ausführung jeweiliger Tätigkeit notwendig sind. Deshalb werden folgende Arbeitsgänge unterschieden:
-
- Arbeitsgang – im Betrieb durchgeführt, in dem der Produktionsprozess definiert wird. Zu solchen Vorgängen werden Ressourcen sowie Ressoucenlisten zugeordnet, die für die Ausführung des Arbeitsganges notwendig sind.
- Fremdfertigungs-Arbeitsgang – im externen Betrieb durchgeführt.
- Multi-Site-Produktionsarbeitsgang – in der Niederlassung eines Betriebs durchgeführt.
- Arbeitsplan – der Arbeitsplan enthält alle Arbeitsgänge, die für die Herstellung eines Artikels durchgeführt werden müssen. Die Reihenfolge der Arbeitsgänge im Arbeitsplan und eventuelle Abhängigkeiten der Arbeitsgänge untereinander werden beim Einlasten des Produktionsauftrages berücksichtigt.
- Produktionsplan – der Produktionsplan ist das gemeinsame Element aus Stückliste und Arbeitsplan. Der Produktionsplan ordnet die Materialien aus der Stückliste den einzelnen Vorgängen aus dem Arbeitsplan zu. Der Produktionsplan stellt somit den ganzen zeitlichen Ablauf der Produktion dar.
Das folgende Diagramm zeigt ein Beispiel für den Produktionsprozess:
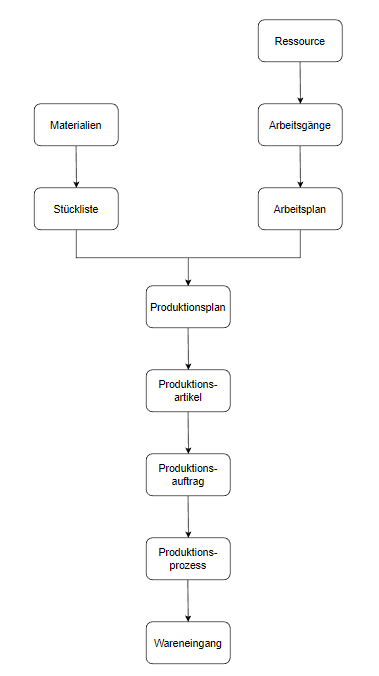
Ein alternatives Produktionsverfahren kann in der Anwendung Artikel, Ansicht Produktion definiert werden. Mit dem alternativen Produktionsverfahren können einem Artikel andere Produktionsstrukturen zugeordnet werden, die zur Produktion des Artikels verwendet werden können. Der Einsatz eines alternativen Produktionsverfahrens kann auch durch Formeln und Bedingungen für die Stückliste, den Arbeitsplan und den Produktionsplan definiert werden. Diese Strukturen werden von der Produktionsauftragsebene aus aufgerufen.
Für jede Anwendung, in der eine Produktionsstruktur definiert werden kann, ist in der Kopfleiste eine Struktursicht verfügbar. Sie ermöglicht die Vorschau aller Ebenen der Produktionsstruktur und die Simulation der für den Produktionsprozess notwendigen definierten Strukturen mit den eingegebenen Parametern.
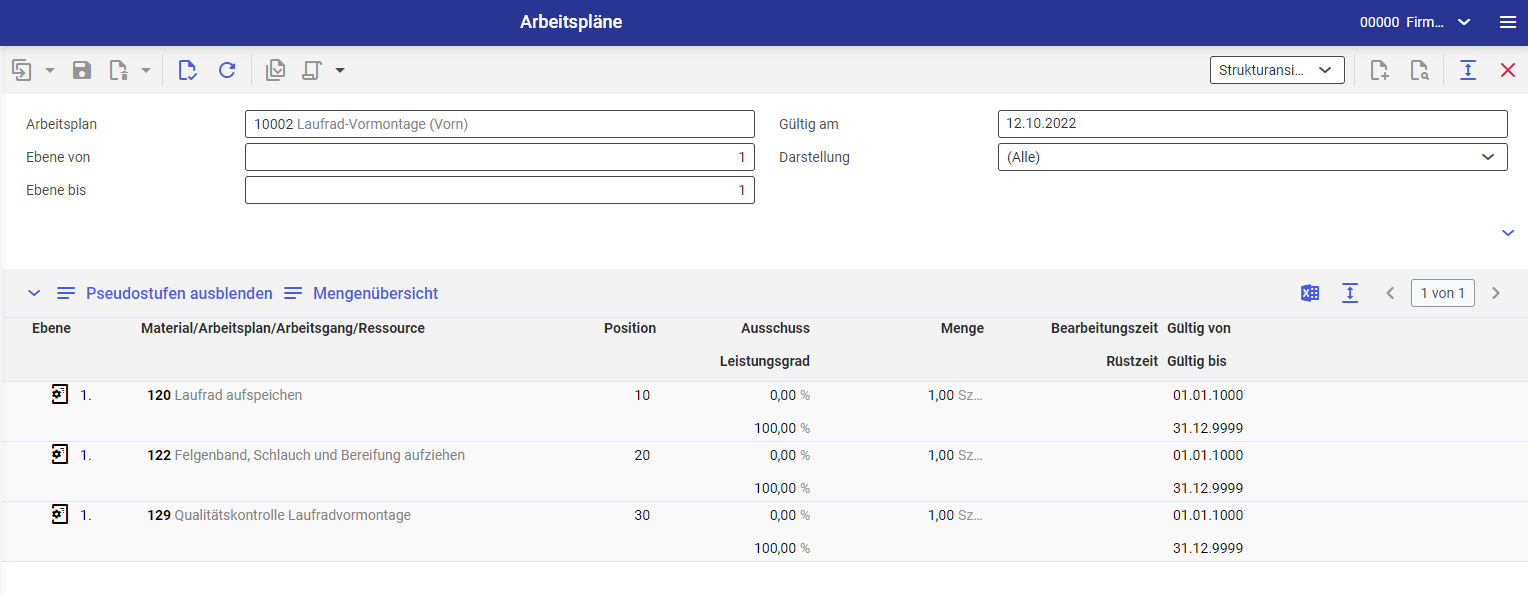
In vielen Fällen sind die Produkte im Laufe ihres Produktionszyklus zahlreichen technischen Änderungen unterworfen. Dazu ist es notwendig, die Änderungen an den Produktionsstrukturen zu folgen. Dazu sind folgende Funktionen zugänglich:
- Produktions-Stammdatenversionierung – ermöglicht es, Versionen der bestehenden Produktionsstrukturen zu definieren, alte Versionen zu sperren und ältere Versionen von Produktionsdaten in der Vorschau anzuzeigen.
- Änderungsnummer – ermöglicht die Definition einer Nummer für hinzugefügte Produktionsdaten, z. B. für ein zu einer Arbeitsgangs-Nummer hinzugefügte Ressource, die die an den Produktionsdaten vorgenommene Änderung definiert.
Ressourcen
Für die Durchführung des Produktionsprozesses sind die Ressourcen ein wesentliches Element., die in den einzelnen Phasen des Produktionsprozesses eingesetzt werden. Als Ressourcen sind Maschinen, Menschen, aber auch Strom oder Wasser zu verstehen, die für den Produktionsprozess erforderlich sind. Im System können Ressourcen gemäß dem folgenden Schema definiert werden:
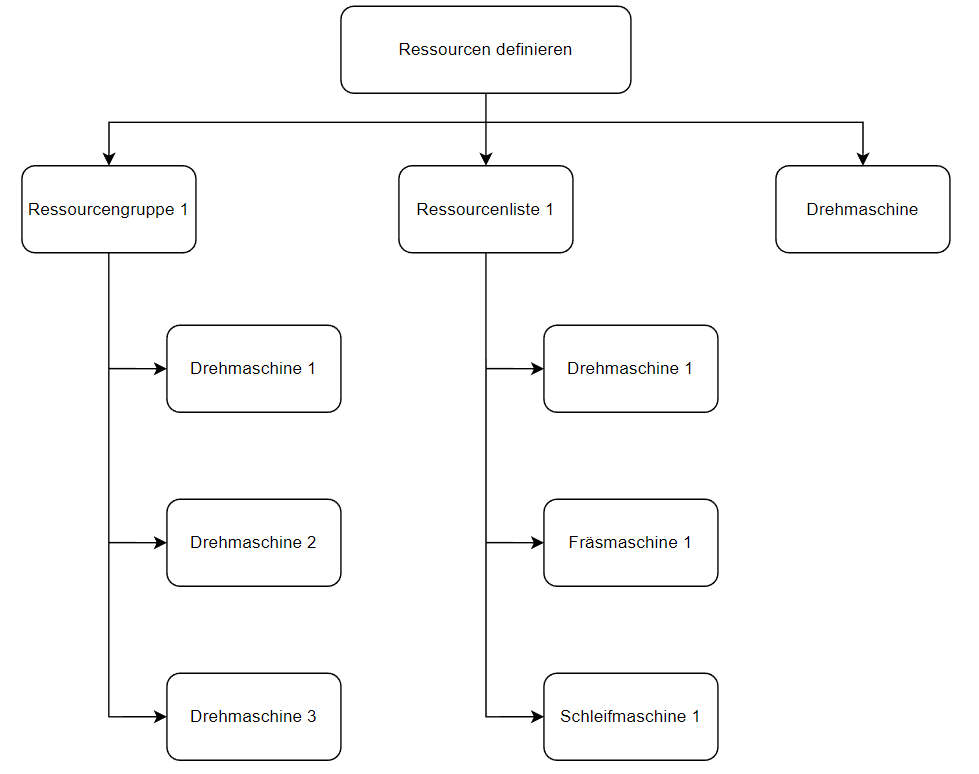
- Ressourcen – die vom Betrieb in der Produktion eingesetzten Mittel.
- Stückliste – ermöglicht die Zuordnung von Ressourcen verschiedener Typen zu einer Definition. Sie ermöglich z. B. die Definition einer Fertigungszelle.
- Ressourcengruppe – ermöglicht die Erstellung einer Ressourcengruppe von dem gleichen Typ. Die Ressourcengruppe ermöglicht eine effektivere Verwaltung der Ressourcenkapazitäten.
Die Ressourcen werden den Kostenstellen zugewiesen, damit die Kosten für ihre Arbeit bewertet werden können. Außerdem können sie in einem zeitlich begrenzten oder zeitlich unbegrenzten Modus arbeiten, in dem der Benutzer ihnen eine beliebige Arbeitseinheit zuweisen kann. So können zeitunabhängige Ressourcen definiert werden, z. B. Strom oder Wasser. Jede Ressource hat ein bestimmtes Leistungsgrad, auf dessen Grundlage ihr Einsatz geplant wird.
Um eine effizientere Verwaltung der Ressourcen im System zu ermöglichen, stehen die folgenden Anwendungen zur Verfügung:
- Ressourcenkapazität – ermöglicht es, die Arbeitszeit der Ressource anzuzeigen und zu bearbeiten
- Ressourcenbelegung – ermöglicht es, die geplanten Produktionsaktivitäten auf Ressourcen zu überprüfen. Sie ermöglicht die Filterung der Leistung nach Ressourcen, Produktionsaufträgen, Standorten oder Zeiträumen. Sie ermöglicht auch graphische Lieferzuteilung – die Verschiebung eines bestimmten Produktionsvorgangs innerhalb der Pufferzeit.
- Ressourcenauslastung – ermöglicht es, die Nutzung der für die Produktion verfügbaren Ressourcen zu bewerten. Sie stellt die verbrauchte Arbeitszeit der Ressource im Verhältnis zur verfügbaren Zeit in grafischer oder tabellarischer Form zusammen. Sie ermöglicht das Filtern der Kapazität nach Ressourcen, Kostenstellen, Standorten, Zeiträumen oder Materialbedarfsplanung.
Produktionsprozess organisieren
Zeiten in der Produktion
Die Organisation und Verwaltung der Produktion erfordert die Festlegung von Produktionszeiten im System, sowie die Erstellung von Produktionsunterlagen und die Unterstützung von Hintergrund-Anwendungen.
Die Produktionszeit wird im Werkskalender definiert, einschließlich der Arbeits- und arbeitsfreien Tage. Die Erstellung des Zeitplans, auf dessen Grundlage die Produktion geplant wird, ist im folgenden Diagramm dargestellt:
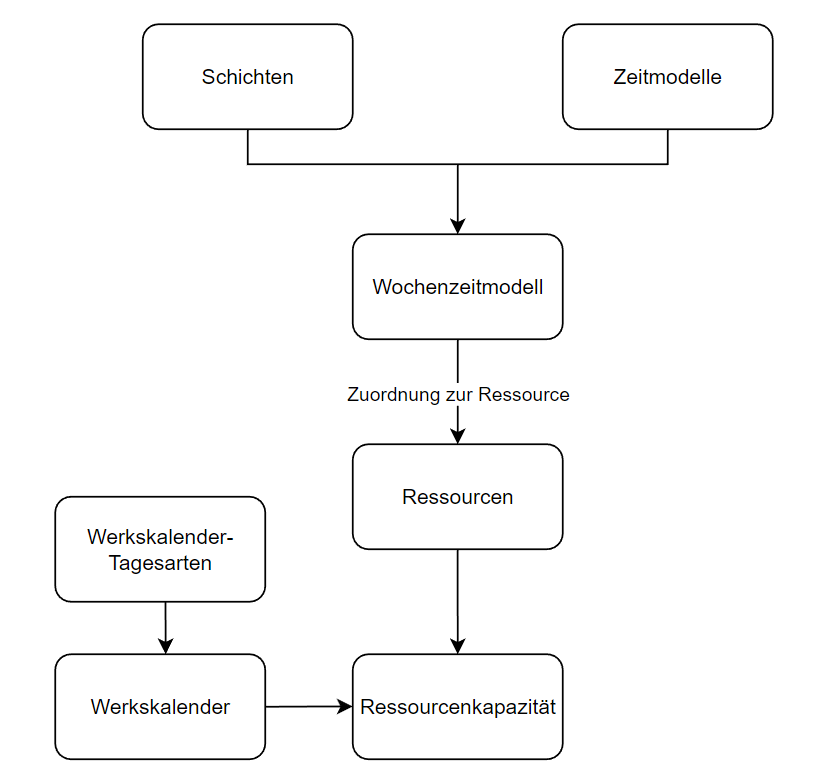
Schichten – in Verbindung mit dem Zeitmodell ist die Schichte eine bestimmte Arbeitszeit
Zeitmodelle – ermöglicht die Festlegung von Arbeitszeitintervallen, z. B. 6:00 – 9:30, 10:00 – 14:00
Wochenzeitmodell – ermöglicht es, Daten aus den Anwendungen Schichten und Zeitmodelle zu verbinden und dann diese Daten den Wochentagen zuzuordnen. Ein Zeitmodell wird einer Ressource zugeordnet, was die Arbeitsplanung und -Leistung ermöglicht.
Produktionsbelege
Im Modul Produktion sind folgende Produktionsbelege zu unterscheiden:
- Dokumente eines Produktionsverfahren – Belege, die mit dem zu ausführendem Produktionsauftrag verbunden sind
- Materialbelege – Logistikbelege zur materiellen Sicherung des Produktionsverfahrens
- Arbeitsbelege – Dokumente über die Tätigkeiten im Produktionsverfahren
- Fremdfertigung-Lieferauftrag – Dokumente, die das Fremdfertigungsverfahren betreffen
Das folgende Diagramm zeigt ein Beispiel für das Produktionsverfahren, in denen die Prozessdokumentation erstellt wird:
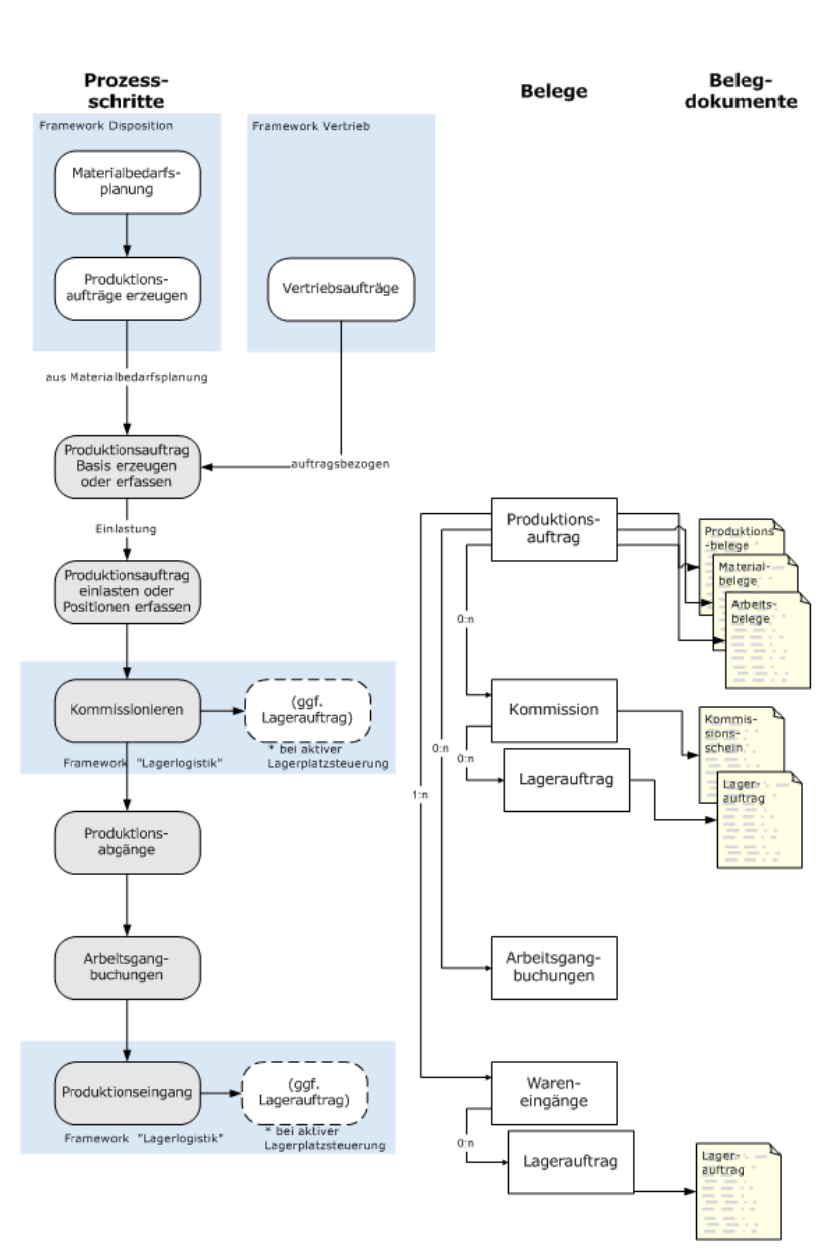
Zusätzlich können je nach Definition des Produktionsverfahrens verwandte Dokumente für einen Produktionsauftrag erzeugt werden:
- Vertriebsaufträge – wenn der Produktionsauftrag aus einem Vertriebsauftrag erzeugt wurde (manuell oder automatisch für konfigurierte Artikel).
- Produktkalkulationen – wenn ein konfigurierter Artikel automatisch kalkuliert wurde oder eine Auftragskalkulation manuell mit einem Produktionsauftrag verknüpft wurde.
- Beschaffungsaufträge – wenn Fremdfertigungs-Arbeitsgänge im Produktionsauftrag enthalten sind und der Produktionsauftrag bereits eingelastet wurde.
- Wareneingänge aus der Produktion – aufgrund der Fertigmeldung (und Zugangsbuchung) des Produktions-Artikels und zugehöriger Kuppelprodukte.
- Kommissionen der Produktion – aufgrund der Umlagerung der Einsatzmaterialien vom Hauptlager in das Produktionslager.
- Verteilaufträge – wenn der Auftrag interne Fremdfertigungs-Arbeitsgänge beinhaltet.
Hintergrund-Anwendung
Die Hintergrund-Anwendungen ermöglichen das Verwalten, Löschen, Aktivieren oder Übertragen der in das System eingegebenen Daten. Während des Betriebs kann der Benutzer den Prozess im Hintergrund ausführen lassen, so dass das System ohne Unterbrechung weiterarbeiten kann. Die folgenden Hintergrund-Anwendungen sind im Modul Produktion verfügbar:
- Produktionsverfahren aktivieren – beim ersten Start des Systems wird die Funktion Produktionsverfahren aktiviert, die es ermöglicht, das Produktionsverfahren für einen Artikel zum Zeitpunkt des Produktionsauftrags auszuwählen.
- Produktions-Stammdaten reorganisieren – ermöglicht die Entfernung von Produktionsstrukturen, die mit einer Löschkennzeichen versehen sind.
- Menge von zusammengehörigen Formeln und Bedingungen reorganisieren – ermöglicht das direkte Löschen von Datensätzen in der Datenbank, die sich auf definierte Formeln und Bedingungen beziehen.
- Service-Stücklisten reorganisieren – ermöglicht das Löschen der Stücklisten, die mit einem Löschkennzeichen versehen sind.
- Produktionsaufträge reorganisieren – ermöglicht das Löschen von Produktionsaufträgen sowie der verknüpften Reservierungen, die mit dem Löschkennzeichen versehen sind.
- Ressourcen reorganisieren – ermöglicht das Löschen von Ressourcen, die mit dem Löschkennzeichen versehen sind.
- Ressourcengruppen reorganisieren – ermöglicht das Löschen von Ressourcengruppen , die mit dem Löschkennzeichen versehen sind.
- Produktionsvorschläge reorganisieren – ermöglicht das Löschen von Produktionsvorschlägen, die mit dem Löschkennzeichen versehen sind.
- Produktionsplanstrukturen prüfen – ermöglicht die Überprüfung von Produktionsstrukturen anhand zyklischer Referenzen.
- Änderungsverlauf für Produktionsaufträge erzeugen – ermöglicht den Export von Produktionsauftragsdaten für die Kostenrechnung in CFE (Comarch Financial Enterprise).
- Änderungsverlauf für Produktionsaufträge aktualisieren – ermöglicht die Aktualisierung von Produktionsauftragsdaten, die für die Kostenrechnung in CFE (Comarch Financial Enterprise) verwendet werden.
Produktionsauftrag
Produktionsauftrag ist das Basiselement eines Produktionsablaufes. Er enthält die Anforderung an die Produktion, Materialien bzw. Leistungen zu einem bestimmten Termin in einer bestimmten Menge herzustellen bzw. zu erbringen. Der Produktionsauftrag legt fest, mit welchen Arbeitsgängen bzw. Ressourcen und mit welchen Einsatzmaterialien eine festgelegte Artikelmenge zu einem bestimmten Termin zu produzieren ist.
Die Grundeinstellungen der erzeugten Produktionsaufträge werden in der Produktions-Auftragsart in der Anwendung Produktions-Auftragsarten festgelegt.
Die Produktions-Auftragsart enthält eine Reihe von Einstellungen, die für die jeweilige Fertigungsauftragsart als vordefiniert konfiguriert werden können. Sie werden zur Identifizierung von Produktionsaufträgen und zur Definition von Voreinstellungen verwendet. In den Produktions-Auftragsarten gibt es außerdem eine Menge von Daten, die für die Logistik, die Buchhaltung oder zur Einschränkung der Berechtigungen an andere Organisationen verwendet werden.
Ein Produktionsauftrag, der auf der Produktions-Auftragsart basiert, kann:
- manuell über die Anwendung Produktionsaufträge erstellt werden
- über die Duplizierung eines vorhandenen Produktionsauftrags in der Anwendung Produktionsaufträge erstellt werden
- auf Basis von einem Vertriebsauftrag erstellt werden
- auf Basis von einem Produktionsvorschlag erstellt werden
Ein Beispiel für Verarbeitung eines Produktionsauftrages wurde im Folgenden dargestellt:
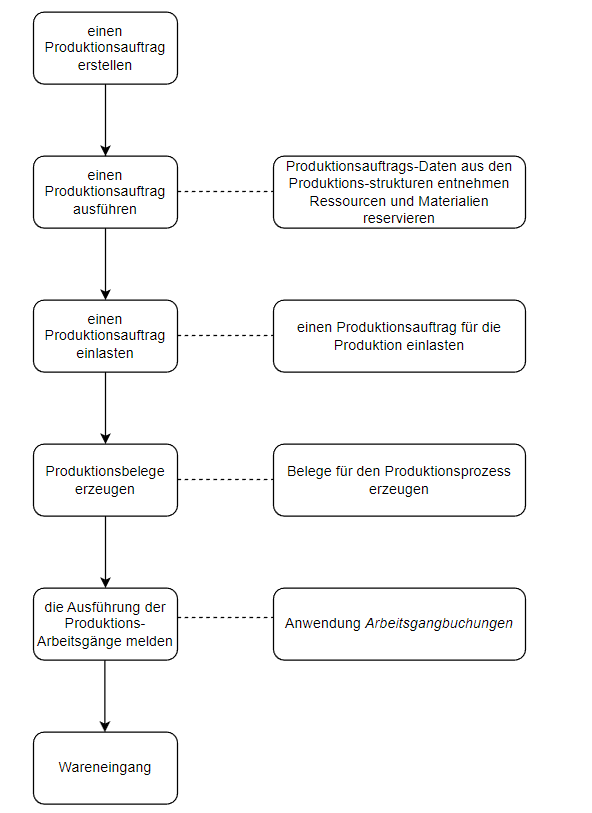
Die Produktionsprozesse beginnen mit der Erstellung eines Produktionsauftrags, umfassen die Einlastung und schichtgenaue Terminierung des Auftrages, die Kapazitätsvergabe, die Steuerung und Planung bis hin zum Rückmelden aller wichtigen Informationen aus den Betriebsdaten. Verfügbare Kapazitäten werden variabel durch die Zuordnung der Kapazitätsprofile für Ressourcen in Wochenzeitmodellen (Zeitmodellzuordnung, Schichtmodell) ermittelt. Wenn es nicht möglich ist, ein festes Wochenzeitmodell für bestimmte Ressourcen zuzuordnen, die bei Bedarf zur Verfügung stehen oder benötigt werden, ist es möglich, die verfügbare Produktionskapazität für ein Schicht- oder Zeitmodell mit Hilfe der Anwendung Ressourcenkapazitäten flexibel zu definieren.
Einlastung eines Produktionsauftrags hat dies zur Folge:
- für alle aktuellen Materialpositionen der Stückliste werden Material-Reservierungen erzeugt, die sich aud die Verfügbarkeitsrechnung auswirken
- für alle aktuellen Kuppelproduktionspositionen der Stückliste werden Kuppelproduktionspositionen erzeugt
- für alle aktuellen Arbeitsgänge des Arbeitsplanes werden Arbeitsgangpositionen erzeugt
- für alle aktuellen Ressourcen werden Ressourcen-Reservierungen erzeugt
- für Fremdfertigungs-Arbeitsgangpositionen werden Beschaffungsaufträge erzeugt
Auf Basis des Produktionsauftrages werden die Arbeitsbelege erzeugt. Der Ausdruck der Arbeitsbelege sollte nach Abschluss der Bearbeitung des Produktionsauftrags erfolgen. Sonst müssen die Arbeitsbelege neu erstellt werden.
Das Rückmelden erfolgen über die Anwendungen: Arbeitsgangbuchungen, Produktionsabgänge und Wareneingänge. Die Rückmeldungen können auch durch Betriebsdaten-Erfassungsgeräte erfolgen, z. B. über entsprechende Importschnittschellen.
Auf Basis dieser Rückmeldungen erfolgt die Entlastung der reservierten Materialien und Ressourcen, die Buchung der daraus entstehenden Material- und Leistungsbewegungen sowie die Bereitstellung dieser Daten für den Produktionsauftrag.
Die Information über den Status eines Produktionsauftrags gilt als eine zusätzliche Auskunft. Die Status werden für den ganzen Produktionsauftrag und für die einzelnen Positionen des Auftrags eingesetzt. Mit dieser Information kann sich der Nutzer in dem aktuellen Bearbeitungsstatus eines Produktionsauftrags orientieren.
Die Planung eines Produktionsauftrags wird maßgeblich durch die Wahl der Terminierungsart beeinflusst, die den Produktionsprozess auf Basis des End- oder Starttermins einplant, je nach den gewählten Terminen und der Verfügbarkeit der Ressourcen. Eine ausführliche Beschreibung der Planungsarten finden Sie in dem Artikel Einlastung.
Die Gruppenverwaltung von Produktionsaufträgen erfolgt in Anwendungen vom Typ Cockpit. Für Produktionsaufträge sind folgende Anwendungen verfügbar:
- Cockpit: Produktionsaufträge/Einlastungsfehler
- Cockpit: Produktionsaufträge
- Cockpit: Produktionsaufträge/Arbeitspositionen
- Cockpit: Produktionsaufträge/Materialpositionen
Buchhaltung
Die Rückmeldung innerhalb der Produktion erfolgt in den Buchhaltungs-Anwendungen. Die eingegebenen Daten zu den gemeldeten Arbeitsgangs-Positionen und Materialreservierungen werden in den Produktionsauftrag übernommen. Die folgenden Hintergrund-Anwendungen sind im Modul Produktion verfügbar, in denen die Rückmeldung zu Produktionsaufträgen erfolgt:
- Produktionsabgänge – hier können die für die Produktion verwendeten Materialien für einen Produktionsauftrag gemeldet werden
- Arbeitsgangbuchungen – hier können die Betriebsdauer und die produzierten Mengen gemeldet werden, die einem Produktionsauftrag zugeordnet wurden
- Ausschussbuchungen – hier können Ausschüsse eines Fertigprodukts für einen Produktionsauftrag gemeldet werden
- BDE-Buchungen – hier kann mit der Schnittstelle für die Rückmeldungen verbunden werden, die ermöglicht, die Echtzeitberichte über die Produktionsaufträge zu liefern
Um die Verwaltung der Arbeitsgang-Buchungen zu optimalisieren, stehen folgende Anwendungen vom Typ Cockpit zur Verfügung:
- Cockpit: Arbeitsgangbuchungen
- Cockpit: BDE-Buchungen
Fremdfertigung
Im Modul Produktion können Sie die Fremdfertigungs-Arbeitsgänge definieren. Es werden folgende Fremdfertigungs-Arbeitsgangs-Arten unterschieden:
- externe Fremdfertigung
Auslöser für einen Fremdfertigungsprozess sind ein oder mehrere Fremdfertigungs-Arbeitsgänge in einem Produktionsauftrag Beim Einlasten des Produktionsauftrages werden automatisch Beschaffungsbelege erzeugt. Der Beschaffungsauftrag enthält Informationen darüber, was an welchen externen Fremdfertiger für die Fremdfertigung geschickt werden soll. Der gesamte Fremdfertigungsprozess sowie die Lieferung an den Fremdfertiger wird mithilfe der Anwendung Fremdfertigungs-Arbeitsgangbuchungen gesteuert.
- Multi-Site-Produktionsarbeitsgang
Werden Produktionsprozesse innerhalb der eigenen Organisation auf verschiedene Standorte verteilt, dann müssen diese Produktionsstufen jeweils pro Produktionsstandort festgelegt werden.
Die Standorte, die verschiedenen Firmen angehören, erfordern:
- verschiedene Kostenstellen der Ressourcen
- verschiedene Kostensätze
- die Erstellung separater Arbeitsgänge für Standorte
Bei Stücklisten müssen sie:
- mindestens einmal für einen Standort erfasst werden.
- lediglich eine Lagerlogistikorganisation haben, die diese bearbeiten darf.
Die Stücklisten sind nur dann organisationsspezifisch, wenn in ihnen bereits Lagerorte für die Materialabgänge oder der Zugangslagerort festgelegt wird.
Stücklisten können im Unterschied zu den Arbeitsplänen, Arbeitsgängen und Ressourcen auch für andere Standorte verwendet oder auch auf andere Standorte dupliziert werden.
Dazu muss sichergestellt werden, dass das Material auch auf dem Ziel-Standort mindestens Lagerlogistikdaten besitzt, auf den dupliziert werden soll.
Das Material und die entstandenen Halbfabrikate werden zwischen den Produktionsstandorten bewegt, entweder per Verteilauftrag oder per einfacher Materialbuchung. In der Materialbedarfsplanung können dafür automatisch die Verteilvorschläge für das Material erzeugt werden, je nach den Einstellungen, die in der Anwendung Artikel, Ansicht Planung definiert werden.
Da der Fremdfertigungs-Artikel über keine Lagerlogistikdaten verfügt, kann ein entstandenes Halbfabrikat nicht über den Wareneingang auf das eigene Lager zurückgebucht werden
Im Folgenden werden die Multi-Site- und externer Produktionsarbeitsgang dargestellt:
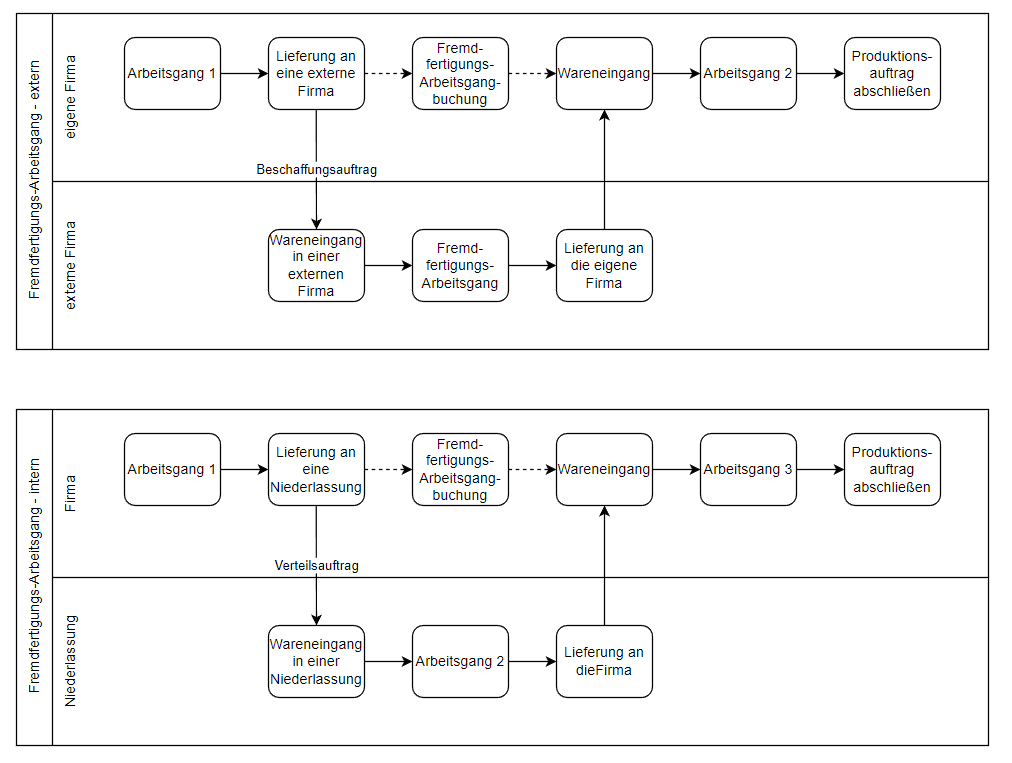
Customizing
Muss ein Produkt erfasst werden, dessen endgültige Definition z. B. im Beschaffungsauftrag erstellt, so steht im System eine Produktkonfigurationsfunktion zur Verfügung. Im System können Regeln definiert werden, mit denen ein Produkt konfiguriert wird. Der Produkt-Konfigurator ist ein grafisches Dialogfeld, in dem Sie erforderliche Merkmale eines Artikels auswählen können, um die endgültige Definition eines Produkts zu erstellen.
Ein Diagramm zur Erstellung von Produktkonfigurationsregeln ist im Folgenden abgebildet:
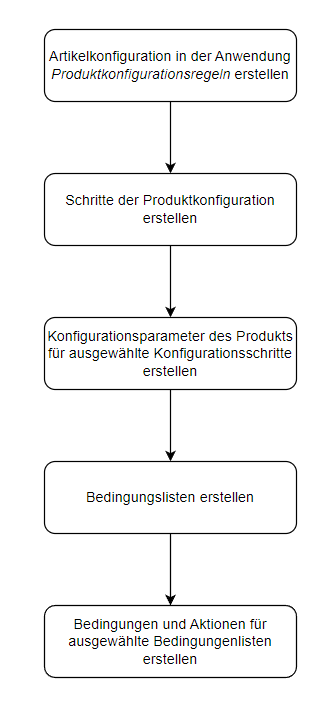
Der Produktionsprozess für den konfigurierbaren Artikel ist in der nachstehenden Abbildung dargestellt:
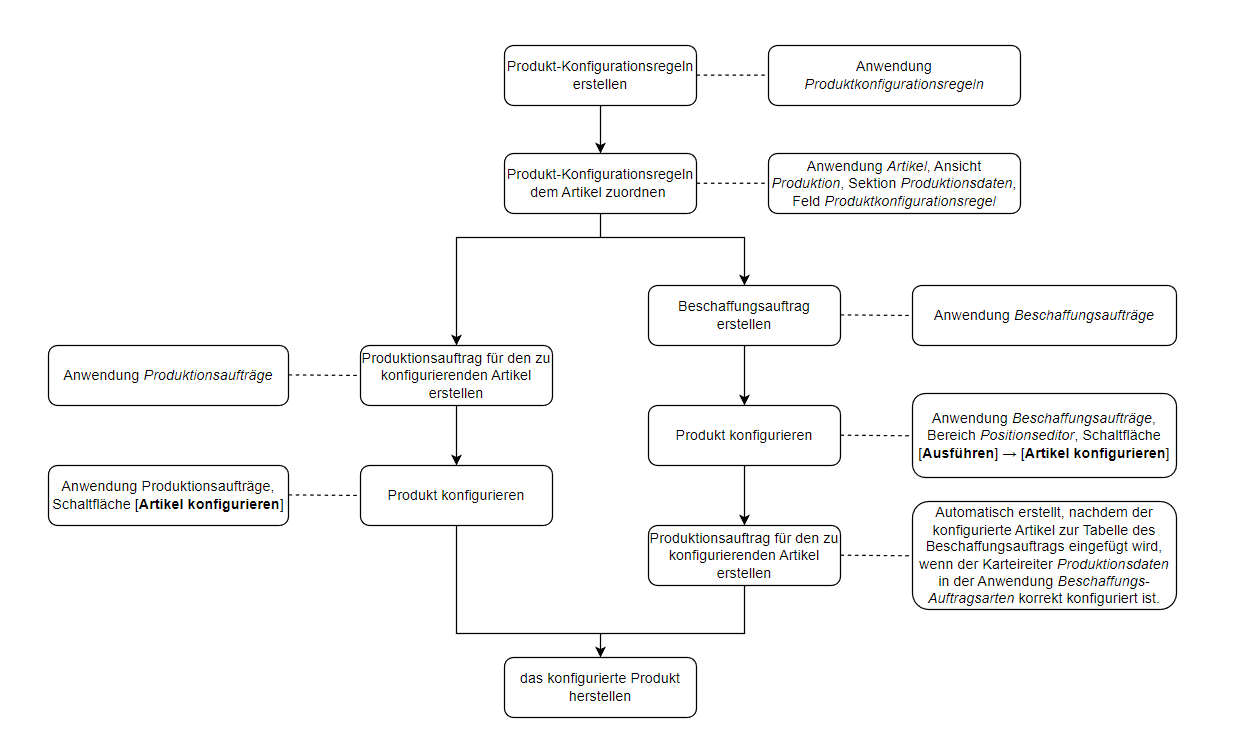
Artikelausprägung
Artikel können mithilfe von Identifizierungen verwaltet werden. Die Identifizierungen dienen zur eindeutigen Erkennung von Artikeln. Folgende produktionsrelevante Identifizierungen können genutzt werden:
- Los
- Charge/Serie
- Seriennummer mit Bestandsführung
- Seriennummer ohne Bestandsführung
In einigen Branchen ist eine Information über die in der Produktion verwendeten Identifizierungen der Materialien notwendig (Chargen-Rückverfolgung). Verfügt ein Produktions-Artikel über eine Identifizierung, dann wird eine Nachweis- und Verwendungsspezifikation aufgebaut.
Die Artikelausprägungen können verwendet werden, um:
- Informationen über die Herkunft eines Artikels zu liefern.
- Informationen über den Verlauf eines Produktionsprozesses zu liefern.
Für konfigurierte Artikel, die alle dieselbe Artikelnummer besitzen, aber trotzdem unterschiedliche Eigenschaften aufweisen, kann über die Spezifikation eine zusätzliche Identifikation vergeben werden.
Kuppelprodukte
Kuppelprodukte können im Produktionsprozess auf verschiedenen Produktionsstufen anfallen. Kuppelprodukte sind Lagerartikel, die beim Wareneingang gebucht werden, wenn ein Produktions-Artikel auf das Lager gebucht wird. Kuppelprodukte können auch in der Produktionskalkulation entsprechend mit Anteilen der Produktionskosten belastet werden.
Sie werden als Material vom Bestand abgebucht und nach der Produktionsfertigmeldung wieder in den Bestand als Kuppelprodukt zurückgebucht.
Bei Kuppelprodukten lässt sich im Produktionsauftrag ein Fertigungstermin für den Artikel angeben. Dieser Termin wird in der Materialverfügbarkeit als geplanter Zugang berücksichtigt.
Bestandswert berechnen
Die Berechnung des Wertes der Bestandswerte ermöglicht es, den Wert der Materialien zu ermitteln, die derzeit in Produktionsprozessen verarbeitet werden, die nocht nicht gefertigt werden. Materialien, die sich in Produktionsprozessen befinden, sind nicht auf Lager sichtbar , so dass ihr Wert nicht überprüft werden kann. Die folgenden Anwendungen werden für die oben beschriebene Tätigkeit im System verwendet:
- Produktions-Bestandswerte berechnen – ermöglicht es, die Prozessdaten für die Berechnung des Materialwerts (Preise, Termine) zu definieren und den Prozess für bestimmte Positionen, Klassifizierungen, Kostenträger oder Fertigungsaufträge einzugrenzen. Die Berechnung ist ein Hintergrundprozess, der über die Schaltfläche [Bewertung der Bestandswerte, die sich im Produktionsprozess befinden] gestartet werden muss.
- Produktions-Bestandswerte abfragen – ermöglicht es, die Ergebnisse der Berechnung der Produktions-Bestandswerte zu sehen.
Besonderheiten
Bei komplexen Produktionsprozessen können Sie im System:
- die Parameter verwenden – dies sind benutzerdefinierte Felder, die für Arbeitsgänge und Ressourcen definiert werden. Diese können in den erstellten Bedingungen, Formeln oder Ersatzfunktionen verwendet werden, durch die die Eigenschaften des Produktionsprozesses verändert werden.
- Bedingungen, Formeln und Ersatzfunktionen erstellen – dies sind mathematische Formeln und vorgefertigte Funktionen, die im System definiert sind, um Änderungen der Produktionsprozessparameter in Abhängigkeit von ausgewählten Eingangsdaten zu automatisieren, z. B. die Verwendung von Artikeln in einer Stückliste je nach den gewählten Artikelfarbvariante.
Die ausführlichen Informationen über die Funktionalitäten des Produktionsmoduls finden Sie auf der Hilfe-Seite des Produkts unter der Kategorie Produktion.